图书介绍
金相分析原理及技术PDF|Epub|txt|kindle电子书版本网盘下载
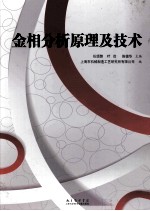
- 任颂赞,叶俭,陈德华主编 著
- 出版社: 上海:上海科学技术文献出版社
- ISBN:9787543957343
- 出版时间:2013
- 标注页数:1142页
- 文件大小:770MB
- 文件页数:1165页
- 主题词:金相技术
PDF下载
下载说明
金相分析原理及技术PDF格式电子书版下载
下载的文件为RAR压缩包。需要使用解压软件进行解压得到PDF格式图书。建议使用BT下载工具Free Download Manager进行下载,简称FDM(免费,没有广告,支持多平台)。本站资源全部打包为BT种子。所以需要使用专业的BT下载软件进行下载。如BitComet qBittorrent uTorrent等BT下载工具。迅雷目前由于本站不是热门资源。不推荐使用!后期资源热门了。安装了迅雷也可以迅雷进行下载!
(文件页数 要大于 标注页数,上中下等多册电子书除外)
注意:本站所有压缩包均有解压码: 点击下载压缩包解压工具
图书目录
第一篇 金属学及热处理原理基础2
第1章 金属和合金的结构2
1.1 晶体中原子间的键合2
1.1.1 金属键2
1.1.2 共价键2
1.1.3 离子键3
1.1.4 范德瓦耳斯键3
1.1.5 混合键4
1.2 晶体结构基础4
1.2.1 晶系和布拉菲点阵4
1.2.2 晶面指数和晶向指数5
1.2.3 晶带和晶带定律7
1.2.4 晶面间距7
1.3 金属的晶体结构8
1.3.1 典型的金属晶体结构8
1.3.2 3种晶体结构的特征9
1.4 合金相的晶体结构11
1.4.1 合金的组元、相及组织11
1.4.2 固溶体12
1.4.3 中间相结构14
1.4.4 超结构(有序固溶体)17
1.5 晶体缺陷17
1.5.1 点缺陷17
1.5.2 线缺陷18
1.5.3 面缺陷20
参考文献21
第2章 合金相图23
2.1 单元系相图和金属结晶23
2.1.1 单元系相图和同素异构转变23
2.1.2 纯金属结晶24
2.2 二元系合金相图和合金的结晶27
2.2.1 匀晶相图和合金的结晶28
2.2.2 共晶相图和合金的结晶31
2.2.3 包晶相图和合金的结晶33
2.2.4 共析相图35
2.2.5 二元系合金相图的应用35
2.3 Fe-Fe3C和Fe-C相图和应用37
2.3.1 铁碳合金的基本相37
2.3.2 铁碳合金的平衡结晶过程和组织38
2.4 三元系合金相图简介42
2.4.1 三元系合金相图基本构成42
2.4.2 Fe-N-C三元系相图实例43
参考文献44
第3章 钢在加热及冷却过程中的组织转变45
3.1 钢在加热过程中的组织转变45
3.1.1 钢中奥氏体的形成45
3.1.2 奥氏体的形成方式及影响因素47
3.1.3 奥氏体晶粒长大及影响因素49
3.2 钢在冷却过程中的组织转变50
3.2.1 过冷奥氏体的等温转变50
3.2.2 过冷奥氏体的连续冷却转变52
3.2.3 过冷奥氏体的珠光体转变53
3.2.4 过冷奥氏体的马氏体转变58
3.2.5 过冷奥氏体的贝氏体转变67
3.3 淬火钢回火时的组织转变74
3.3.1 淬火钢回火时的组织转变75
3.3.2 马氏体回火后的组织76
3.3.3 淬火钢回火后力学性能变化77
3.3.4 钢中贝氏体的回火转变78
3.3.5 淬火钢的回火脆性78
3.4 其他固态相变简介79
3.4.1 调幅分解转变79
3.4.2 合金的时效强化转变81
参考文献81
第4章 合金元素在钢中的作用83
4.1 合金元素与铁的交互作用83
4.1.1 合金元素对Fe-M相图影响83
4.1.2 合金元素与铁的交互作用84
4.1.3 硼和铁的交互作用85
4.2 合金元素与碳的交互作用85
4.2.1 形成碳化物的稳定程度85
4.2.2 形成碳化物的类型85
4.2.3 碳化物的相互溶解及作用87
4.3 合金元素间相互作用和金属间化合物87
4.3.1 金属间化合物87
4.3.2 合金元素与氮的交互作用90
4.4 合金元素与钢中晶体缺陷交互作用91
4.5 合金元素对Fe-Fe3C状态图的影响92
4.5.1 改变共析温度(A1)92
4.5.2 改变共析含碳量92
4.5.3 改变奥氏体的最大溶碳量92
4.6 合金元素对钢热处理过程中组织转变的影响93
4.6.1 合金元素对钢加热转变的影响93
4.6.2 合金元素对钢冷却转变的影响94
4.6.3 合金元素对淬火钢回火转变的影响96
4.7 合金元素对钢力学性能的影响98
4.7.1 合金元素对退火(或正火)状态下钢的力学性能的影响98
4.7.2 合金元素对淬火回火状态下钢的力学性能的影响99
4.7.3 合金元素对钢在高温及低温时力学性能的影响100
4.8 合金元素在钢中的分布100
附录102
参考文献104
第二篇 金相分析常用技术106
第5章 金相显微镜及应用106
5.1 金相显微镜分类及基本组成106
5.1.1 金相显微镜的分类106
5.1.2 金相显微镜的基本组成107
5.2 光学的基本概念及显微放大原理107
5.2.1 光的基本特性107
5.2.2 光的反射和折射108
5.2.3 反射镜和棱镜110
5.2.4 透镜及成像原理110
5.2.5 透镜的像差112
5.2.6 金相显微镜放大原理和光学特点114
5.3 金相显微镜的基本组件114
5.3.1 物镜115
5.3.2 目镜119
5.3.3 照明系统119
5.3.4 光阑121
5.3.5 滤光片121
5.3.6 显微镜镜架系统123
5.3.7 显微摄像系统124
5.3.8 偏光、相衬等其他附件125
5.4 金相显微镜主要技术参量125
5.4.1 显微镜的总有效放大率125
5.4.2 金相显微镜的分辨力、工作距离127
5.4.3 主要几何尺寸127
5.4.4 实际视场128
5.5 金相显微镜的几种观察方法128
5.5.1 明场观察129
5.5.2 暗场观察129
5.5.3 偏振光观察130
5.5.4 微分干涉相衬观察132
5.6 金相显微摄影操作要点133
5.6.1 样品要求133
5.6.2 操作要求133
5.7 金相显微镜的安装、检定及维护133
5.7.1 金相显微镜的安装133
5.7.2 金相显微镜的检定133
5.7.3 金相显微镜的品质及维护134
5.8 典型金相显微镜介绍135
5.8.1 全自动金相显微镜136
5.8.2 电动金相显微镜136
5.8.3 普及型金相显微镜136
参考文献136
第6章 定量金相及金相图像分析系统137
6.1 体视学简介137
6.2 定量金相技术138
6.2.1 半定量测量——比较法138
6.2.2 定量测量方法138
6.2.3 定量测量的误差统计分析140
6.3 定量金相测量试样要求141
6.4 金相图像分析系统141
6.4.1 金相数字图像定量测量基本方法142
6.4.2 金相图像分析基本构成143
6.4.3 数字成像过程的控制144
6.4.4 数字图像处理高级技术146
6.4.5 图像分析系统发展148
6.5 金相图像分析中图像处理基本操作技术149
6.5.1 定义标尺149
6.5.2 图像清晰处理150
6.5.3 图像灰度调整151
参考文献152
第7章 显微硬度试验及应用153
7.1 显微维氏(Vickers)硬度试验153
7.1.1 试验原理及计算公式153
7.1.2 维氏压头及试验法的特点154
7.1.3 试验方法和注意事项156
7.1.4 试样最小厚度与最大检测力间的关系156
7.1.5 显微维氏硬度计性能要求及检定系统159
7.1.6 维氏硬度试验测量结果不确定度的评定161
7.1.7 维氏显微硬度试验的应用161
7.1.8 钢铁、有色合金、难熔化合物组成相的显微硬度值164
7.2 努氏(Knoop)硬度试验166
7.2.1 试验原理及计算公式167
7.2.2 检测方法和注意事项167
7.2.3 试样最小厚度与试验力间关系169
7.2.4 努氏硬度计性能要求170
7.2.5 努氏硬度试验的应用171
7.3 显微维氏和努氏硬度试验方法及压头的比较172
7.3.1 试验压头的比较172
7.3.2 试验方法及应用比较173
7.4 影响显微硬度试验结果的因素174
7.4.1 硬度计的影响174
7.4.2 试样的影响175
7.4.3 操作的影响175
7.4.4 压痕异常判断176
7.5 显微硬度计177
7.5.1 哈纳门(Hanemann)型显微硬度计177
7.5.2 早期手动显微硬度计178
7.5.3 数显式显微硬度计179
7.5.4 半自动硬度测量的显微硬度计179
参考文献180
第8章 金相试样的制备181
8.1 金相试样的选取及截取181
8.1.1 金相试样的选取181
8.1.2 金相试样的截取182
8.2 金相试样的夹持及镶嵌183
8.2.1 金相试样的夹持183
8.2.2 金相试样的镶嵌184
8.3 金相试样的磨光186
8.3.1 磨光机理186
8.3.2 磨光用材料187
8.3.3 磨光方法187
8.4 金相试样的抛光189
8.4.1 机械抛光189
8.4.2 电解抛光193
8.4.3 化学抛光196
8.5 显微组织的显示197
8.5.1 化学浸蚀197
8.5.2 电解浸蚀199
8.5.3 特殊显示方法199
8.6 非钢铁金属的制样及组织显示方法203
8.7 现场金相及金相复型技术204
8.7.1 现场金相制样205
8.7.2 金相复型技术205
附录:常用金相抛光浸蚀试剂206
参考文献207
第9章 扫描电子显微镜及应用208
9.1 扫描电子显微镜工作基础208
9.1.1 背散射电子208
9.1.2 二次电子209
9.1.3 透射电子209
9.1.4 特征X射线209
9.1.5 俄歇电子210
9.2 扫描电子显微镜结构及工作原理210
9.2.1 扫描电子显微镜结构210
9.2.2 扫描电子显微镜各种图像的成像原理211
9.3 X射线波谱仪214
9.3.1 X射线波谱仪的结构原理214
9.3.2 X射线波谱仪的分析方式216
9.3.3 X射线波谱定量分析216
9.4 X射线能谱仪218
9.4.1 能谱分析的原理218
9.4.2 能谱仪的结构218
9.4.3 X射线能谱分析219
9.4.4 X射线波谱和X射线能谱分析的特点219
9.5 电子通道效应及电子背散射衍射221
9.5.1 电子通道效应221
9.5.2 背散射电子衍射(EBSD)222
9.6 新颖扫描电镜简介223
9.6.1 高分辨场发射扫描电镜223
9.6.2 低电压扫描电镜和低真空扫描电镜224
9.7 扫描电子显微镜的试样制备方法224
9.7.1 金属断口试样的制备225
9.7.2 金相试样的制备225
9.7.3 导电性差和不导电试样制备226
9.7.4 粉末试样的制备226
9.8 典型应用227
9.8.1 断裂和断口分析227
9.8.2 金相显微组织分析229
9.8.3 金属及合金表面形貌分析231
9.8.4 粉末颗粒的测定和纳米材料的研究232
9.8.5 晶体取向研究232
9.8.6 动态观察233
参考文献233
第10章 透射电子显微镜及应用234
10.1 透射电子显微镜原理234
10.1.1 电子的性质234
10.1.2 电磁透镜234
10.1.3 电子显微镜的分辨力237
10.1.4 透射电子显微镜的场深和焦深237
10.2 透射电子显微镜的构造238
10.2.1 镜筒238
10.2.2 真空系统240
10.2.3 供电系统240
10.3 透射电镜的样品制备技术240
10.3.1 表面形貌复型及投影技术240
10.3.2 萃取复型243
10.3.3 粉末样品制备方法244
10.3.4 金属薄膜样品制备方法245
10.4 复型像分析及应用247
10.4.1 复型图像分析247
10.4.2 金相显微组织形态分析248
10.4.3 现场检验分析中的应用249
10.4.4 失效分析中的应用250
10.5 电子衍射分析及应用251
10.5.1 电子衍射原理251
10.5.2 电子显微镜中的电子衍射253
10.5.3 电子衍射花样分析253
10.5.4 电子衍射在金相分析中的应用256
10.6 金属薄膜衍衬像及应用257
10.6.1 衍衬成像原理257
10.6.2 衍衬像分析应用257
10.7 分析电子显微镜及应用260
10.7.1 透射扫描电子显微镜260
10.7.2 薄晶体X射线显微分析260
10.7.3 动态分析260
10.7.4 高分辨电子显微分析261
10.7.5 分析电镜应用实例261
参考文献262
第11章 X射线衍射及在金属分析中的应用263
11.1 X射线衍射的基本原理263
11.1.1 晶体结构的基本特点263
11.1.2 晶体对X射线的衍射265
11.1.3 X射线衍射的结构分析267
11.2 X射线衍射仪的构造267
11.2.1 X射线粉末衍射仪267
11.2.2 多功能衍射仪269
11.3 X射线衍射在金属分析中的一些应用271
11.3.1 物相定性分析271
11.3.2 宏观(残余)应力的测定274
11.3.3 点阵常数的测定277
11.3.4 物相定量分析281
11.3.5 织构的测定283
11.3.6 晶体结构的测定287
11.3.7 衍射线形的分析287
11.3.8 表面与薄膜分析290
11.4 多晶体衍射全谱线形拟合法与晶体结构的测定293
11.4.1 Rietveld全谱线形拟合法的基本概念294
11.4.2 Rietveld全谱线形拟合精修结构应用举例295
11.4.3 晶体结构的从头测定296
11.4.4 全谱线形拟合法在粉末衍射传统领域中的应用简介297
11.5 同步辐射与X射线分析简介300
11.5.1 同步辐射的特性300
11.5.2 同步辐射装置构造简介301
11.5.3 上海光源的X射线分析技术简介301
参考文献304
第三篇 金相常规项目检测308
第12章 钢铁材料的低倍检验308
12.1 钢锭结晶过程及缺陷形成308
12.2 钢的酸蚀试验方法及缺陷评定309
12.2.1 试样的截取及制样310
12.2.2 热酸蚀试验311
12.2.3 冷酸蚀试验312
12.2.4 钢的低倍组织缺陷及评定原则313
12.3 连铸钢坯凝固组织及内部缺陷的评定320
12.3.1 连铸钢坯凝固组织低倍评定方法321
12.3.2 连铸钢坯低倍组织缺陷评级322
12.4 低倍组织浸蚀方法的应用323
12.5 断口试验及缺陷鉴别324
12.5.1 检验断口的制备324
12.5.2 检验用断口的分类325
12.5.3 断口形貌及各种缺陷识别325
12.6 钢材塔形发纹检验329
12.6.1 发纹的特征及成因330
12.6.2 塔形发纹检验试样制备330
12.6.3 发纹检验方法330
12.7 钢材硫印、磷印试验331
12.7.1 磷印试验331
12.7.2 硫印试验332
参考文献332
第13章 钢的显微组织常规分析及评定333
13.1 带状组织评定333
13.2 游离渗碳体分布评定335
13.3 魏氏组织评定337
13.4 碳化物不均匀度评定339
13.4.1 共晶碳化物的不均匀度评定339
13.4.2 二次共析碳化物偏聚评定346
13.5 碳化物液析评定348
13.6 钢材表面脱碳层鉴别与深度测定350
13.7 球化退火处理及球化级别评定351
13.7.1 共析、过共析钢球化退火及评级351
13.7.2 亚共析钢球化退火及评级353
13.8 高温使用中(珠光体)球化程度评定356
13.8.1 20号系列钢珠光体球化评级(DL/T 674—1999)356
13.8.2 12CrlMoV钢球化评级(DL/T 773—2001)357
13.8.3 15CrMo类钢珠光体球化评级(DL/T 787—2001)358
13.8.4 2.25Cr-1Mo类钢球化评级(DL/T 999—2006)359
参考文献360
第14章 钢中非金属夹杂物检测及评级361
14.1 钢中非金属夹杂物的种类及形态361
14.1.1 按夹杂物的化学成分分类361
14.1.2 按夹杂物的可塑性分类363
14.1.3 按夹杂物的来源分类363
14.1.4 按夹杂物形态和分布分类364
14.2 钢中非金属夹杂物的鉴定方法364
14.2.1 金相分析法364
14.2.2 电子探针方法368
14.2.3 电解分离法368
14.3 钢中非金属夹杂物显微检测评定方法368
14.3.1 非金属夹杂物显微检测的取样与观察369
14.3.2 GB/T 10561—2005(ISO 4967:1998)检测方法370
14.3.3 原DIN 50 602:1985检测方法375
14.3.4 ASTM E45-2011a检测方法379
14.3.5 BS EN 10247:2007检测方法381
14.3.6 钢材纯洁度级别检测383
参考文献384
第15章 金属材料晶粒度测定385
15.1 金属材料晶粒度及晶粒度级别385
15.1.1 晶粒度的基本概念385
15.1.2 几种晶粒度级别的定义386
15.2 常用晶粒度级别测定方法389
15.2.1 比较法389
15.2.2 面积法393
15.2.3 截点法393
15.2.4 测定报告394
15.3 几种金属材料晶粒度级别的测定394
15.3.1 低碳钢冷轧薄板铁素体晶粒度的测定394
15.3.2 铜及铜合金晶粒度的测定397
15.3.3 铝及铝合金晶粒度的测定397
15.3.4 高速工具钢晶粒度的测定402
15.4 双重晶粒度的测定方法402
15.4.1 双重晶粒度分布类别402
15.4.2 双重晶粒度级别的测定方法403
15.5 晶粒度形成及显示405
15.5.1 铁素体钢奥氏体晶粒度的形成与显示405
15.5.2 高速工具钢奥氏体晶粒的显示407
15.5.3 常用显示奥氏体晶粒浸蚀剂407
参考文献408
第四篇 常用金属工程材料及金相分析410
第16章 通用结构钢及金相分析410
16.1 通用结构钢的特性及组成410
16.1.1 通用结构钢的主要特性及影响因素410
16.1.2 通用结构钢的成分组成411
16.1.3 合金元素在结构钢中的作用412
16.2 各种工艺条件下调质结构钢金相分析414
16.2.1 轧制处理及金相分析414
16.2.2 退火处理及金相分析414
16.2.3 锻造及金相分析415
16.2.4 淬火-低温回火及金相分析417
16.2.5 淬火-高温回火(调质)及金相分析418
16.2.6 中温等温处理及金相分析419
16.2.7 拉拔工艺及金相分析422
16.3 非调质机械结构钢及金相分析422
16.3.1 非调质机械结构钢的成分和工艺特点423
16.3.2 铁素体-珠光体非调质钢及金相分析426
16.3.3 贝氏体型非调质钢427
16.3.4 冷作强化非调质钢及金相分析430
16.4 通用结构钢常见组织缺陷及诊断430
16.4.1 过热及过烧组织431
16.4.2 表面脱碳432
16.4.3 淬火(调质)组织中存在铁素体433
16.4.4 开裂434
16.4.5 其他缺陷组织434
参考文献435
第17章 弹簧钢及金相分析436
17.1 弹簧及弹簧钢436
17.1.1 弹簧的分类及主要特性436
17.1.2 弹簧钢的性能要求436
17.1.3 弹簧钢所含合金元素及作用437
17.2 弹簧钢原材料加工及金相分析442
17.2.1 热轧弹簧钢型材及金相分析442
17.2.2 冷拉弹簧钢型材及金相分析442
17.2.3 预强化弹簧钢丝及金相分析442
17.3 弹簧成型后的热处理及金相分析444
17.3.1 弹簧成型后的基本热处理及金相分析444
17.3.2 几种常用弹簧钢的热处理及金相分析446
17.4 弹簧的表面处理452
17.4.1 表面化学保护层452
17.4.2 弹簧表面的金属防护层452
17.5 弹簧钢的缺陷组织和判别453
17.5.1 弹簧常见的表面缺陷453
17.5.2 弹簧钢的显微组织缺陷454
参考文献456
第18章 轴承钢及金相分析457
18.1 轴承钢的分类457
18.1.1 高碳铬轴承钢459
18.1.2 表面硬化轴承钢459
18.1.3 高碳铬不锈轴承钢460
18.1.4 高温轴承钢461
18.1.5 其他轴承材料462
18.2 高碳铬轴承钢的成分与冶金质量463
18.2.1 化学成分的控制463
18.2.2 低倍组织缺陷464
18.2.3 原材料微观缺陷的检验466
18.3 高碳铬轴承钢在加热和冷却时的组织转变470
18.3.1 高碳铬轴承钢在加热过程中的组织转变470
18.3.2 高碳铬轴承钢在冷却过程中的组织转变471
18.4 高碳铬轴承钢的锻造及组织472
18.4.1 高碳铬轴承钢的锻造472
18.4.2 锻件的显微组织473
18.4.3 锻造缺陷474
18.5 高碳铬轴承钢热处理及金相组织475
18.5.1 正火476
18.5.2 球化退火476
18.5.3 淬火、回火478
18.5.4 等温淬火回火处理481
18.5.5 深冷处理482
18.6 其他轴承钢热处理及金相组织简介483
18.6.1 高温轴承钢的热处理及金相组织483
18.6.2 高碳铬不锈轴承钢热处理及金相组织485
18.6.3 表面处理轴承钢热处理及金相组织486
18.7 轴承零件常见失效形式及诊断486
18.7.1 轴承零件的磨削烧伤及诊断486
18.7.2 轴承零件接触疲劳失效及诊断487
参考文献488
第19章 工具钢及金相分析489
19.1 工具钢分类及基本特性489
19.1.1 工具钢分类489
19.1.2 工具钢基本特性489
19.2 碳素工具钢及金相分析490
19.2.1 碳素工具钢的牌号及特点490
19.2.2 碳素工具钢原材料的金相分析491
19.2.3 碳素工具钢热处理及金相分析493
19.3 合金工具钢及金相分析496
19.3.1 合金工具钢牌号及化学成分496
19.3.2 合金工具钢原材料的金相分析496
19.3.3 合金工具钢热处理及金相分析498
19.4 高速工具钢及金相分析500
19.4.1 高速工具钢组成、牌号及分类500
19.4.2 高速工具钢原材料金相分析503
19.4.3 高速工具钢热处理及金相分析510
19.5 高速工具钢表面改性及金相分析517
19.5.1 蒸汽处理518
19.5.2 氧氮化处理518
19.5.3 硫氮共渗蒸汽处理的复合处理519
19.5.4 高速钢的渗氮处理520
19.5.5 高速钢的PVD镀层520
19.6 工具钢的缺陷分析522
19.6.1 原材料缺陷522
19.6.2 制坯工艺不当造成的缺陷525
19.6.3 热处理不当造成的缺陷527
19.6.4 其他因素造成的缺陷530
参考文献530
第20章 模具钢及金相分析531
20.1 模具钢分类531
20.2 冷作模具钢及金相分析532
20.2.1 冷作模具钢特性及组成532
20.2.2 冷作模具钢原材料金相检验533
20.2.3 冷作模具钢的热处理及金相检验535
20.3 热作模具钢及金相分析540
20.3.1 热作模具钢特性及组成540
20.3.2 热作模具钢的原材料金相检验542
20.3.3 热作模具钢的热处理及金相检验543
20.4 塑料模具专用钢及金相分析550
20.4.1 塑料模具钢的特性及组成550
20.4.2 预硬型塑料模具专用钢的热处理及金相检验551
20.4.3 时效硬化型塑料模具钢热处理及金相检验552
20.5 模具钢的缺陷组织及诊断554
20.5.1 组织偏析554
20.5.2 碳化物偏析554
20.5.3 淬火欠热及过热过烧组织554
20.5.4 淬火组织中的贝氏体555
参考文献556
第21章 不锈钢和耐热钢及金相分析557
21.1 不锈钢特性、分类及牌号557
21.1.1 不锈钢耐腐蚀原理和合金元素的作用557
21.1.2 不锈钢的分类558
21.1.3 不锈钢牌号的命名559
21.2 马氏体不锈钢和耐热钢及金相分析561
21.2.1 马氏体不锈钢和耐热钢的牌号、成分及性能561
21.2.2 马氏体不锈钢及耐热钢合金化的特点562
21.2.3 马氏体不锈钢和耐热钢的热处理及金相组织565
21.3 奥氏体不锈钢和耐热钢及金相分析571
21.3.1 奥氏体不锈钢和耐热钢的牌号、成分及特点571
21.3.2 奥氏体不锈钢合金化特点574
21.3.3 奥氏体不锈钢的热处理576
21.3.4 奥氏体不锈钢的金相检验577
21.4 铁素体不锈钢和耐热钢及金相分析582
21.4.1 铁素体不锈钢和耐热钢的牌号、成分及性能582
21.4.2 铁素体不锈钢和耐热钢合金化特点584
21.4.3 铁素体不锈钢的热加工及金相组织585
21.4.4 铁素体不锈钢的脆化现象585
21.5 双相不锈钢及金相分析586
21.5.1 双相不锈钢的特点和分类、牌号586
21.5.2 双相不锈钢中的合金化特点588
21.5.3 双相不锈钢的热加工工艺及对组织、性能的影响588
21.5.4 双相不锈钢的组织及金相检验589
21.6 沉淀硬化型不锈钢及金相分析592
21.6.1 沉淀硬化型不锈钢特点、分类及牌号592
21.6.2 奥氏体-马氏体沉淀硬化不锈钢强化工艺及组织593
21.6.2 马氏体沉淀硬化不锈钢强化工艺及组织594
21.7 不锈钢的腐蚀行为597
21.7.1 不锈钢腐蚀行为及分类597
21.7.2 各类不锈钢的耐腐蚀性能599
21.8 不锈钢和耐热钢的样品制备及相鉴别602
21.8.1 不锈钢和耐热钢金相试样制备602
21.8.2 不锈钢、耐热钢中相的鉴别605
参考文献606
第22章 高温合金及金相分析607
22.1 高温合金特点、分类及牌号表示方法607
22.1.1 高温合金的主要特性607
22.1.2 高温合金的分类608
22.1.3 高温合金的牌号表示方法609
22.1.4 英国和美国的高温合金体系609
22.2 高温合金中各元素的特性和作用610
22.2.1 基体元素的特性610
22.2.2 合金元素的作用611
22.3 高温合金的强化原理611
22.3.1 固溶强化611
22.3.2 第二相(时效)强化612
22.3.3 晶界强化612
22.3.4 工艺强韧化612
22.4 高温合金常见相及其作用613
22.4.1 高温合金中常见析出相及分类613
22.4.2 高温合金中几何密排相及其作用614
22.4.3 拓扑密排相(TCP)618
22.4.4 间隙相620
22.5 高温合金的热处理624
22.5.1 固溶处理624
22.5.2 中间处理624
22.5.3 时效处理625
22.5.4 弯曲晶界热处理625
22.5.5 高温合金的退火处理625
22.6 高温合金的金相组织626
22.6.1 铁基变形高温合金及金相组织626
22.6.2 镍基变形高温合金及金相组织631
22.6.3 钴基变形高温合金及金相组织636
22.6.4 铸造高温合金及金相组织636
22.7 高温合金的金相分析637
22.7.1 高温合金的金相制样及相鉴别637
22.7.2 变形高温合金的组织评定642
附录648
参考文献649
第23章 铸钢及金相分析650
23.1 铸钢的工艺特点650
23.1.1 铸钢件的成型及其组织性能特点650
23.1.2 铸钢件的常规热处理特点652
23.2 铸造碳钢及其金相分析653
23.2.1 铸造碳素钢的牌号和化学成分653
23.2.2 铸造碳素钢的金相分析654
23.3 铸造低合金钢及其金相分析656
23.3.1 一般工程与结构用低合金铸钢件656
23.3.2 铸造低合金结构钢的金相组织659
23.4 铸造不锈钢及金相分析663
23.4.1 铸造不锈钢分类、牌号及其化学成分663
23.4.2 铸造马氏体不锈钢665
23.4.3 铸造奥氏体不锈钢及金相分析666
23.4.4 铸造奥氏体铁素体双相不锈钢670
23.4.5 铸造马氏体沉淀硬化不锈钢672
23.4.6 铸造不锈钢的腐蚀形式673
23.5 铸造奥氏体锰钢及其金相分析673
23.5.1 铸造奥氏体锰钢的化学成分674
23.5.2 合金元素在奥氏体锰钢中的作用674
23.5.3 奥氏体锰钢的热处理676
23.5.4 奥氏体锰钢的力学性能677
23.5.5 铸造奥氏体锰钢的金相分析677
23.5.6 铸造奥氏体锰钢的常见缺陷680
23.6 铸钢的缺陷组织及诊断682
23.6.1 铸造热裂纹682
23.6.2 铸造冷裂纹684
23.6.3 缩孔和缩松684
23.6.4 气体类缺陷685
23.6.5 夹砂和夹渣685
23.6.6 焊补缺陷685
参考文献686
第24章 铸铁及金相分析687
24.1 铸铁的分类及其牌号687
24.2 铸铁的石墨化过程688
24.2.1 铁-碳合金双重相图和Fe-C-Si三元相图688
24.2.2 铸铁的石墨化过程689
24.2.3 影响铸铁石墨化的因素691
24.3 灰铸铁及金相分析692
24.3.1 灰铸铁的牌号及性能692
24.3.2 灰铸铁的石墨评定694
24.3.3 灰铸铁中的组织及分级698
24.4 球墨铸铁及金相分析701
24.4.1 球墨铸铁牌号及性能701
24.4.2 球状石墨的特性和结构703
24.4.3 球墨铸铁的石墨评级704
24.4.4 球墨铸铁的组织及分类705
24.5 可锻铸铁及金相分析706
24.5.1 可锻铸铁牌号及性能706
24.5.2 可锻铸铁的石墨化机理707
24.5.3 可锻铸铁的金相检验708
24.6 蠕墨铸铁及金相分析710
24.6.1 蠕墨铸铁牌号及其性能710
24.6.2 蠕墨铸铁的蠕墨化过程710
24.6.3 蠕墨铸铁的金相检验710
24.7 特种铸铁及金相组织711
24.7.1 减摩铸铁及金相组织712
24.7.2 抗磨铸铁及金相组织714
24.7.3 耐热铸铁及金相组织717
24.7.4 耐蚀铸铁及金相组织719
24.7.5 奥氏体铸铁及金相组织720
24.8 铸铁常见缺陷及诊断720
24.8.1 由气体引起的缺陷720
24.8.2 针孔722
24.8.3 缩孔722
24.8.4 石墨偏析723
24.8.5 组织的不均匀性724
24.8.6 夹杂、夹渣724
24.8.7 热裂、冷裂725
参考文献725
第25章 粉末冶金材料及金相分析726
25.1 粉末冶金材料概述726
25.1.1 粉末冶金材料的分类726
25.1.2 粉末冶金材料的牌号、成分及性能726
25.2 粉末冶金制品的工艺特点732
25.2.1 金属粉末的制取方法732
25.2.2 粉末冶金制品的成形方法732
25.2.3 粉末冶金制品的固结734
25.2.4 粉末冶金材料的熔渗和浸渗处理735
25.2.5 硬质合金生产的工艺特点736
25.3 铁基粉末冶金制品的热处理736
25.3.1 铁基粉末冶金制品的热处理特点736
25.3.2 铁基粉末冶金制品的整体淬火、回火处理737
25.3.3 铁基粉末冶金制品的渗碳及碳氮共渗737
25.3.4 铁基粉末冶金制品的氮碳共渗737
25.3.5 铁基粉末冶金制品的烧结硬化737
25.3.6 铁基粉末冶金制品的水蒸气处理738
25.4 粉末冶金制品的金相分析738
25.4.1 粉末冶金材料金相制样的特点738
25.4.2 粉末冶金制品中孔隙、石墨及夹杂等检测741
25.4.3 粉末冶金制品的金相组织及评定743
25.5 硬质合金的金相分析746
25.5.1 硬质合金金相制样特点747
25.5.2 硬质合金的孔隙及非化合碳(石墨)检测748
25.5.3 硬质合金的金相组织评定750
25.5.4 硬质合金的组织缺陷753
参考文献754
第26章 铝、铝合金及金相分析755
26.1 铝合金的分类、成分和牌号755
26.1.1 纯铝的特性及牌号755
26.1.2 铝合金中主要合金元素及作用756
26.1.3 变形铝合金的分类及牌号758
26.1.4 铸造铝合金分类、牌号及成分759
26.1.5 铝合金工艺状态代号760
26.2 铝合金的热处理762
26.2.1 铝合金的均匀化退火763
26.2.2 铝合金的回复与再结晶退火763
26.2.3 铝合金的固溶处理765
26.2.4 铝合金的时效765
26.2.5 铝合金的回归现象及回归处理766
26.2.6 铝合金的冷(冷热循环)处理766
26.2.7 铸造铝合金热处理及力学性能766
26.2.8 变形铝合金热处理及力学性能767
26.3 铸造铝合金的金相分析768
26.3.1 Al-Si系铸造铝合金及金相分析768
26.3.2 Al-Cu系铸造铝合金及金相分析776
26.3.3 Al-Mg系铸造铝合金及金相分析780
26.3.4 Al-Zn系铸造铝合金及金相分析781
26.3.5 Al-Re系铸造铝合金及金相分析782
26.4 变形铝合金的金相分析783
26.4.1 1×××系铝合金及金相分析783
26.4.2 2×××系铝合金及金相分析784
26.4.3 3×××系铝合金及金相分析786
26.4.4 4×××系铝合金及金相分析787
26.4.5 5×××系铝合金及金相分析787
26.4.6 6×××系铝合金及金相分析789
26.4.7 7×××系铝合金及金相分析790
26.5 铝合金的相鉴别及试样制备791
26.5.1 铝合金金相试样制备特点792
26.5.2 铝合金相的鉴别793
26.6 铝及铝合金晶粒度的测定797
26.7 铝合金的常见缺陷及诊断797
26.7.1 铝合金的常见铸造缺陷及诊断797
26.7.2 变形铝合金压力加工低倍组织缺陷及诊断800
26.7.3 铝合金热处理缺陷及判断804
26.7.4 铝合金的腐蚀及诊断806
参考文献807
第27章 铜、铜合金及金相分析808
27.1 铜及铜合金的合金化以及分类、牌号808
27.1.1 铜的合金化808
27.1.2 铜及铜合金的分类808
27.1.3 铜及铜合金牌号命名808
27.2 铜及铜合金的热处理811
27.2.1 退火811
27.2.2 淬火和回火813
27.3 纯铜及金相分析814
27.3.1 纯铜的牌号和化学成分814
27.3.2 微量合金元素对纯铜组织及性能影响814
27.3.3 纯铜的金相组织及评定817
27.4 黄铜及金相分析819
27.4.1 黄铜的分类、牌号和化学成分819
27.4.2 普通黄铜的组织与性能821
27.4.3 复杂黄铜的组织与性能824
27.4.4 黄铜的金相评定830
27.5 青铜及金相分析830
27.5.1 锡青铜及金相分析830
27.5.2 铝青铜及金相分析835
27.5.3 铍青铜及金相分析840
27.5.4 硅青铜及金相组织844
27.5.5 其他青铜及金相分析845
27.6 白铜及金相分析846
27.6.1 白铜的代号和化学成分846
27.6.2 普通白铜及金相组织848
27.6.3 复杂白铜及金相组织849
27.7 铜及铜合金的缺陷组织及判别850
27.7.1 铜及铜合金的“氢病”850
27.7.2 应力腐蚀开裂(季裂)850
27.7.3 黄铜的脱锌及脱铝腐蚀851
27.7.4 晶粒粗大、不均匀852
27.7.5 锡汗852
27.8 铜及铜合金金相制样特点852
27.8.1 铜及铜合金的抛光852
27.8.2 铜及铜合金的组织显示853
参考文献855
第28章 钛、镁、锌及合金的金相分析856
28.1 钛及钛合金的金相分析856
28.1.1 钛及钛合金的特性、分类及牌号856
28.1.2 钛合金的相变及热处理861
28.1.3 钛及钛合金的金相组织866
28.1.4 钛及钛合金金相制样特点870
28.2 镁及镁合金的金相分析871
28.2.1 镁及镁合金的特性、分类及牌号871
28.2.2 镁合金的热处理879
28.2.3 镁及镁合金的表面处理884
28.2.4 镁合金的金相组织886
28.2.5 镁及镁合金的制样特点及组织判定888
28.3 锌及锌合金的金相分析893
28.3.1 锌及锌合金的特性、分类及牌号893
28.3.2 锌合金的热处理899
28.3.3 锌及锌合金的金相组织及制样特点900
参考文献903
第五篇 几种工艺条件下的金相分析906
第29章 钢件渗碳、碳氮共渗及金相分析906
29.1 化学热处理的基本原理906
29.2 钢件渗碳原理及工艺907
29.2.1 气体渗碳原理907
29.2.2 钢件气体渗碳工艺909
29.2.3 渗碳工艺的发展910
29.2.4 钢件渗碳后的热处理工艺911
29.3 渗碳用钢912
29.3.1 渗碳用钢的成分特点912
29.3.2 渗碳用钢系列914
29.3.3 渗碳用钢的质量控制要点914
29.4 钢件渗碳及淬回火后的组织、性能914
29.4.1 钢件渗碳(缓冷)后的组织914
29.4.2 钢件渗碳淬回火后组织及评定916
29.4.3 渗碳层深度测定921
29.4.4 钢件渗碳淬回火后的性能923
29.5 钢件碳氮共渗原理、特点及工艺924
29.5.1 钢件碳氮共渗原理及特点924
29.5.2 钢件碳氮共渗工艺简介925
29.6 钢件碳氮共渗及淬回火后的组织、性能926
29.6.1 钢件碳氮共渗后缓冷的组织926
29.6.2 钢件碳氮共渗淬回火组织及评定926
29.6.3 钢件碳氮共渗层深度测定929
29.6.4 钢件碳氮共渗淬回火后的性能929
29.7 钢件渗碳淬回火及碳氮共渗淬回火的组织缺陷930
参考文献931
第30章 钢件渗氮、氮碳共渗及金相分析932
30.1 钢铁件渗氮基本原理及其工艺932
30.1.1 钢铁件渗氮基本原理及组织932
30.1.2 钢铁件气体渗氮原理及工艺935
30.1.3 钢件渗氮前预处理及渗氮后的冷却938
30.2 渗氮专用钢939
30.2.1 渗氮钢的合金化939
30.2.2 渗氮钢系列941
30.3 钢件气体渗氮后性能941
30.3.1 渗氮件表面硬度及耐磨性941
30.3.2 渗氮件的疲劳强度942
30.3.3 渗氮件的抗腐蚀性942
30.3.4 气体渗氮件表面脆性943
30.4 离子渗氮工艺、组织及性能943
30.4.1 离子渗氮基本原理943
30.4.2 离子渗氮工艺简介944
30.4.3 离子渗氮件的组织及性能945
30.5 氮碳共渗及金相分析945
30.5.1 气体氮碳共渗原理及工艺946
30.5.2 氮碳共渗的组织与性能946
30.6 奥氏体氮碳共渗及金相分析948
30.6.1 奥氏体氮碳共渗原理及工艺948
30.6.2 奥氏体氮碳共渗组织及性能950
30.7 渗氮(氮碳共渗)层深度测定和组织评定951
30.7.1 渗氮(氮碳共渗)层深度测定952
30.7.2 渗氮层组织检验评定954
30.8 渗氮及氮碳共渗的常见缺陷组织957
参考文献959
第31章 渗镀处理及覆盖层的金相分析960
31.1 渗铬及渗铬层的金相分析960
31.1.1 渗铬的工艺及原理960
31.1.2 渗铬层的金相组织与性能961
31.2 渗铝及渗铝层的金相分析964
31.2.1 渗铝的工艺及原理964
31.2.2 渗铝层的金相组织与性能965
31.3 渗锌及渗锌层的金相分析970
31.3.1 渗锌的工艺原理970
31.3.2 渗锌层的金相组织与性能970
31.4 渗硅及渗硅层的金相分析972
31.4.1 渗硅工艺972
31.4.2 渗硅层的金相组织与性能973
31.5 渗硼及渗硼层的金相分析974
31.5.1 渗硼的原理与工艺974
31.5.2 渗硼层的金相组织与性能976
31.6 电镀及电镀层的金相分析980
31.6.1 电镀工艺原理及分类980
31.6.2 电镀层的组织形态及影响因素982
31.6.3 电镀层检测及缺陷组织984
31.7 气相沉积及气相沉积层的金相分析988
31.7.1 物理气相沉积(PVD)基本原理及特点988
31.7.2 化学气相沉积(CVD)基本原理及特点989
31.7.3 气相沉积薄膜组织特点及金相分析989
31.8 热喷涂及热喷涂层的金相分析992
31.8.1 热喷涂的原理和工艺992
31.8.2 常用热喷涂材料993
31.8.3 热喷涂层的金相检验994
31.9 化学转化膜及转化膜的金相分析996
31.9.1 钢铁件的氧化处理及氧化膜金相检验996
31.9.2 铝合金阳极氧化及氧化膜金相检验998
31.9.3 磷化处理及磷化膜金相检验1000
参考文献1002
第32章 感应加热淬火、激光热处理及金相分析1003
32.1 感应加热淬火及金相分析1003
32.1.1 感应加热淬火的基本原理1003
32.1.2 感应加热淬火工艺及特点1006
32.1.3 感应加热淬火的组织和性能1009
32.1.4 钢铁件感应淬火后有效硬化层深度的测定1010
32.1.5 感应加热淬火后的金相检验1012
32.1.6 感应加热淬火的常见缺陷1015
32.2 激光热处理及金相分析1016
32.2.1 激光及特点1016
32.2.2 激光发生器原理1017
32.2.3 热处理用激光器1017
32.2.4 激光热处理工艺1019
32.2.5 激光表面淬火及其组织、性能1020
32.2.6 激光表面淬火金相检验1024
32.2.7 激光表面合金化工艺及组织1025
32.2.8 激光表面熔覆工艺及组织1028
32.2.9 激光表面冲击强化和组织1029
32.2.10 激光热处理常见缺陷1030
参考文献1032
第33章 焊接接头的金相分析1033
33.1 焊接方法分类及特点1033
33.2 焊接接头的宏观组织及宏观检测1034
33.2.1 焊接接头的宏观组织1034
33.2.2 焊接接头的宏观检测1034
33.2.3 熔化焊焊缝宏观缺欠及分类1035
33.3 焊接金属的结晶1037
33.3.1 焊接熔池结晶的特殊性1037
33.3.2 焊缝凝固组织的特征及形成原因1037
33.3.3 焊缝中的偏析1043
33.3.4 焊缝金属的二次组织1044
33.4 焊接热影响区的组织1045
33.4.1 焊接热循环的特点1046
33.4.2 焊接加热时组织转变的特点1046
33.4.3 焊接热影响区的组织1046
33.4.4 分析热影响区组织时应考虑的因素1049
33.4.5 焊接热影响区的性能1051
33.5 焊接接头的开裂分析1054
33.5.1 焊接热裂缝1055
33.5.2 焊接接头的冷裂缝1058
33.6 异种金属材料焊接的金相分析1060
33.6.1 异种金属焊接的熔合区1060
33.6.2 异种金属焊接接头显微组织稳定性1062
33.6.3 异种金属焊接接头的主要缺陷1062
33.7 钎焊工艺及金相分析1063
33.7.1 钎焊的冶金过程1064
33.7.2 钎焊接头的金相组织1065
33.7.3 钎焊接头的主要缺陷1066
33.8 焊接接头试样的组织显示1067
33.8.1 宏观组织显示1067
33.8.2 显微组织显示1068
33.8.3 钎焊试样显示1068
参考文献1069
第六篇 金属构件失效分析概述1072
第34章 金属构件的失效及失效形式1072
34.1 金属构件的失效及分类1072
34.2 金属构件受力类型及服役环境1072
34.2.1 金属构件受力类型1072
34.2.2 环境对金属构件的影响1074
34.3 应力集中与构件失效1074
34.3.1 应力集中与应力集中系数1074
34.3.2 材料的缺口敏感性1075
34.3.3 应力集中对构件失效的影响1076
34.4 残余应力与构件失效1077
34.4.1 金属构件的残余应力1077
34.4.2 残余应力对金属构件失效影响1078
34.5 金属构件失效形式及引发原因1078
34.5.1 金属构件失效形式1078
34.5.2 引发金属构件失效的原因1079
34.5.3 各类失效发生的直接原因1080
参考文献1081
第35章 断口分析基础1082
35.1 断口的分类及分析技术1082
35.1.1 断口的分类1082
35.1.2 断口的保护及清理1083
35.1.3 断口分析用技术1084
35.2 断口的宏观分析1085
35.2.1 宏观断口的观察及记录(拍摄)1085
35.2.2 宏观断口的断口要素1087
35.2.3 宏观断口的特征及分类判断1089
35.3 断口的微观分析1091
35.3.1 断口微观分析方法1091
35.3.2 沿晶断口1091
35.3.3 解理断口1092
35.3.4 准解理断口1094
35.3.5 韧窝断口1095
35.3.6 疲劳断口1096
35.4 几种主要断裂模式下的断口分析1098
35.4.1 韧性断裂及断口分析1098
35.4.2 脆性断裂(低应力)及断口分析1101
35.4.3 疲劳断裂的断口分析1104
参考文献1105
第36章 金属构件主要失效模式的诊断1106
36.1 失效分析的思路、原则和程序1106
36.1.1 失效分析基本思路1106
36.1.2 分析思维过程的基本原则1106
36.1.3 失效分析基本程序1107
36.2 断裂失效的诊断1108
36.2.1 裂纹的分类及走向的诊断1108
36.2.2 三类典型断裂模式特征及诊断1113
36.2.3 断裂的走向及负荷状态的判断1114
36.2.4 断裂诱发因素分析1116
36.3 疲劳断裂失效类型及诊断1118
36.3.1 疲劳断裂的分类1118
36.3.2 机械疲劳失效分类及诊断1119
36.3.3 高周疲劳断裂及低周疲劳断裂的诊断1122
36.3.4 热疲劳失效及诊断1123
36.3.5 金属构件高温疲劳失效及诊断1124
36.4 腐蚀失效的诊断1125
36.4.1 腐蚀失效的基本特征1125
36.4.2 全面腐蚀失效的诊断1125
36.4.3 点腐蚀及诊断1125
36.4.4 缝隙腐蚀及诊断1127
36.4.5 晶间腐蚀及诊断1127
36.4.6 应力腐蚀开裂的诊断1128
36.4.7 氢致损伤(氢脆)失效及诊断1130
36.4.8 腐蚀疲劳失效及诊断1132
36.5 磨损失效及诊断1133
36.5.1 粘着磨损失效及诊断1134
36.5.2 磨粒磨损失效及诊断1135
36.5.3 疲劳磨损失效及诊断1137
36.5.4 微动磨损失效及判断1138
36.6 畸变失效及诊断1140
36.6.1 畸变失效及分类1140
36.6.2 弹性畸变失效及诊断1140
36.6.3 塑性畸变过量失效及诊断1141
36.6.4 高温下的畸变失效1141
参考文献1142