图书介绍
中国材料工程大典 第15卷 材料热处理工程PDF|Epub|txt|kindle电子书版本网盘下载
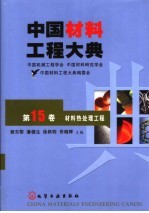
- 樊东黎等主编 著
- 出版社: 化学工业出版社
- ISBN:
- 出版时间:2005
- 标注页数:923页
- 文件大小:105MB
- 文件页数:946页
- 主题词:
PDF下载
下载说明
中国材料工程大典 第15卷 材料热处理工程PDF格式电子书版下载
下载的文件为RAR压缩包。需要使用解压软件进行解压得到PDF格式图书。建议使用BT下载工具Free Download Manager进行下载,简称FDM(免费,没有广告,支持多平台)。本站资源全部打包为BT种子。所以需要使用专业的BT下载软件进行下载。如BitComet qBittorrent uTorrent等BT下载工具。迅雷目前由于本站不是热门资源。不推荐使用!后期资源热门了。安装了迅雷也可以迅雷进行下载!
(文件页数 要大于 标注页数,上中下等多册电子书除外)
注意:本站所有压缩包均有解压码: 点击下载压缩包解压工具
图书目录
第1篇 概论1
1.4 形变热处理3
1.3 化学热处理3
第1章 材料热处理在现代制造业中的地位和作用3
1 热处理工艺种类3
1.1 整体热处理3
1.2 表面热处理3
2.1 提高材料的各种力学性能4
2 提高和发挥材料性能的潜力4
1.5 等离子热处理4
1.6 表面沉积技术4
1.7 镀层复合热处理4
2.4 提高材料的工艺性能5
2.3 提高材料的化学性能5
2.2 提高材料的物理性能5
3 热处理与相邻加工工艺的关系6
1 中国古代的热处理7
第2章 材料热处理技术发展史7
2 中国近代热处理进展9
2.2 科研、开发和新技术应用成果10
2.1 热处理行业现状10
2.3 热处理标准化的进展12
2.4 热处理行业、学术团体13
2.1 可持续发展战略14
2 热处理的总体发展战略14
第3章 热处理技术展望14
1 历史的回顾14
3.1 少无污染15
3 先进热处理技术的发展方向15
2.2 产品质量的不断提高15
2.3 能源的有效利用15
2.4 精确的生产过程15
2.5 高效的生产技术15
3.2 少无畸变17
3.4 少无浪费(能源)19
3.3 少无(质量)分散19
3.5 少无氧化21
4 热处理生产技术改造的途径26
3.8 少无人工26
3.6 少无脱碳26
3.7 少无废品26
4.3 不断提高新技术开发能力27
4.2 知识和技能的再教育27
4.1 设备更新27
参考文献28
第2篇 材料热处理技术基础29
5 常用热处理工艺代号31
4 多工序热处理工艺代号31
第1章 金属热处理工艺分类和代号31
1 基础分类31
2 附加分类31
3 热处理工艺代号31
6 技术要求在零件图样上的表示方法32
1.1 总类38
1 金属热处理工艺术语38
第2章 材料热处理术语38
1.2 退火类39
1.3 淬火类40
1.6 渗碳类41
1.5 固溶热处理类41
1.4 回火类41
1.10 表面处理及复合热处理类42
1.9 共渗类42
1.7 渗氮类42
1.8 渗其他非金属及渗金属类42
1.12 组织类43
1.11 沉积类43
2.1 一般术语44
2 热处理设备术语44
1.13 热处理缺陷类44
2.2 热处理炉通用术语45
2.3 热处理电热设备46
2.6 淬火冷却装置47
2.5 热处理燃料炉47
2.4 热处理炉通用配套设备47
3.3 热处理盐浴用盐类48
3.2 热处理常用气氛类48
2.7 清洗与清理设备48
2.8 其他辅助设备48
3 热处理工艺材料术语48
3.1 总类48
3.6 热处理保护涂料类49
3.5 淬火冷却介质类49
3.4 渗其他非金属剂与渗金属剂及其共渗剂类49
1 Fe-Fe3 C合金相图及其应用51
第3章 合金相图与金属热处理的关系51
2.1 Fe-C合金相图与热处理温度的关系53
2 合金元素对钢铁组织和性能的影响53
2.2 合金元素的影响54
3 其他金属合金相图58
1.2 铁素体-珠光体向奥氏体的等温转变82
1.1 珠光体-奥氏体转变82
第4章 材料热处理的加热82
1 钢在加热过程中的转变82
1.3 连续加热时的奥氏体形成过程83
1.5 钢的晶粒度对性能的影响85
1.4 钢加热时的奥氏体晶粒长大85
1.7 过热和过烧86
1.6 奥氏体晶粒度的显示和测定86
1.8 氧化和脱碳87
2 钢在CO-CO2气氛中的氧化和脱碳89
3 钢在H2-H2 O气氛中的氧化和脱碳91
4 含硫气体对钢的作用92
5.2 加热计算公式及常用图表93
5.1 加热介质分类93
5 加热介质和加热计算93
6.2 制备方法96
6.1 分类及用途96
6 可控气氛96
6.3 炉气控制原理113
6.4 炉气检测方法115
7.1 加热熔盐的成分及用途119
7 加热熔盐和流态床119
7.2 盐浴的脱氧及脱氧剂122
7.4 流态床加热的特点123
7.3 长效盐123
8.1 金属在真空中加热时的行为127
8 真空中的加热127
8.2 金属在真空中的加热速度128
1.1 过冷奥氏体等温转变图129
1 钢的过冷奥氏体转变129
第5章 材料热处理的冷却129
1.3 钢的淬透性和奥氏体连续冷却转变图的关系130
1.2 奥氏体连续冷却转变图130
2.1 马氏体转变的本质131
2 钢在冷却过程中的马氏体转变131
3.2 金属在液态介质中冷却的特征132
3.1 淬火冷却曲线132
2.2 马氏体转变量和转变温度范围132
2.3 马氏体形态132
3 金属热处理的冷却过程132
4.2 Grossmann的淬透性概念133
4.1 概述133
4 钢的淬透性133
4.3 钢淬透性测定方法134
5 淬火冷却方式和淬火介质135
5.1 埋入淬火136
5.2 喷射冷却149
5.3 熔盐等温淬火150
5.4 流态床淬火152
5.5 气冷淬火153
5.6 强烈淬火154
5.7 淬火介质性能测试方法155
5.8 淬火冷却的畸变与开裂156
1 概述159
第6章 热处理工艺材料159
2.2 热处理加热用盐160
2.1 制备气氛的原料气160
2 热处理的加热介质160
3 热处理淬冷介质163
2.4 回火油163
2.3 流动粒子163
3.1 淬火油164
3.2 聚合物淬火剂167
4.2 碳氮共渗剂172
4.1 渗碳剂172
4 热处理渗剂172
7 防渗涂料173
6 不锈钢箔173
4.3 渗硼剂173
4.4 渗金属剂173
5 防氧化脱碳涂料173
9.2 防锈剂174
9.1 清洗剂174
8 表面处理剂174
9 辅助材料174
9.4 催化剂175
9.3 干燥剂和吸收剂175
1.2 热处理工艺性在机械制造工艺过程中的作用和意义176
1.1 零件热处理工艺性的基本概念176
第7章 零件热处理工艺性176
1 概述176
2.1 零件结构177
2 零件热处理工艺性的内容和影响因素177
1.3 零件热处理工艺性的特点177
2.2 零件的材料178
2.3 热处理工艺因素189
2.4 影响零件热处理工艺性的其他因素191
3 改善零件热处理工艺的根本途径192
1 概述194
第8章 材料热处理缺陷、预防和修正194
2.2 加热不当形成的裂纹196
2.1 热处理裂纹形成的机理196
2 热处理裂纹196
2.3 淬火裂纹197
2.4 淬火裂纹的预防方法200
2.5 其他热处理裂纹207
3.1 热处理畸变类型及形成原因208
3 热处理畸变208
3.2 淬火畸变209
3.3 化学热处理畸变214
3.4 热处理变形的校正216
4.1 热处理内应力217
4 残余内应力217
4.2 残余应力对力学性能的影响220
4.3 残余应力的调整和消除222
5 组织不合格223
5.1 氧化与脱碳224
5.2 过热与过烧225
5.4 渗碳组织缺陷227
5.3 低、中碳钢预备热处理球化体级别不合格227
5.5 渗氮组织缺陷229
5.6 渗硼组织缺陷230
6.1 硬度不合格231
6 力学性能不合格231
6.2 拉伸性能不合格232
6.3 持久蠕变性能不合格233
6.4 非铁金属合金力学性能不合格234
6.6 耐腐蚀性能不良235
6.5 疲劳性能不良235
7 脆性236
7.1 回火脆性237
7.2 低温脆性239
7.3 氢脆性240
7.5 渗层脆性243
7.4 σ脆性243
8.1 化学热处理和表面热处理特殊缺陷244
8 其他热处理缺陷244
8.2 真空热处理和加热保护热处理缺陷245
8.3 非铁金属合金热处理缺陷247
1.1 关于热处理的国际标准和国外先进标准251
1 概述251
第9章 材料热处理标准251
2 热处理标准体系表252
1.2 关于全国热处理标准化技术委员会252
2.3 体系表的特点253
2.2 体系表结构及内容253
2.1 制、修订概况253
2.4 热处理专业标准体系明细表254
3 材料热处理标准258
参考文献263
第3篇 材料热处理工艺265
1.1 钢的退火与正火267
1 钢的热处理267
第1章 材料和零件的整体热处理267
1.2 钢的淬火270
1.3 钢的回火279
2.1 铸铁的分类和应用284
2 铸铁的热处理284
2.2 铸铁热处理基础285
2.3 白口铸铁的热处理290
2.4 灰铸铁的热处理291
2.5 球墨铸铁的热处理294
2.6 可锻铸铁的热处理300
1.1 钢在快速加热时的组织转变306
1 表面热处理原理306
第2章 表面热处理306
1.2 钢快速加热对冷却转变的影响308
1.4 表面淬火时的残余应力309
1.3 快速循环加热淬火法制备超细化晶粒309
2.1 火焰加热表面淬火原理及优缺点311
2 火焰加热表面淬火311
2.3 火焰淬火喷嘴312
2.2 火焰的结构及其特征312
2.5 火焰淬火前的准备工作及操作313
2.4 火焰淬火工艺313
2.6 火焰加热表面淬火的应用314
3.1 感应加热的原理315
3 感应加热表面热处理315
3.2 感应器318
3.3 感应加热工艺320
3.4 感应加热淬火的应用324
3.5 感应加热表面淬火后的组织和性能328
4.1 激光的产生及其特点329
4 激光加热表面热处理329
4.2 激光加热表面淬火的表面预处理332
4.5 激光淬火对显微组织结构及性能的影响333
4.4 激光淬火工艺参数选择333
4.3 激光淬火工艺的特点333
4.6 激光淬火层性能335
4.8 激光淬火技术的应用336
4.7 激光淬火加其他强化方法的复合处理工艺336
5.1 电子束加热装置原理337
5 电子束加热表面热处理337
4.9 激光表面重熔337
5.2 电子束和材料的交互作用338
5.3 电子束表面处理的特点339
5.4 电子束表面处理工艺340
1.2 碳在钢中的扩散342
1.1 基本规律342
第3章 化学热处理342
1 原子扩散342
1.3 氮在钢中的扩散343
2.1 气体渗氮344
2 钢的低温化学热处理344
2.2 离子渗氮349
2.3 气体氮碳共渗351
2.4 盐浴硫氮碳共渗354
2.5 渗锌356
2.6 低温化学热处理的渗层组织和性能357
3.1 渗碳和碳氮共渗358
3 钢的高温化学热处理358
3.2 渗硼367
3.3 渗金属369
3.4 钢铁热浸铝和渗铝372
1.3 形变热处理的工业应用377
1.2 形变热处理的基本原理377
第4章 形变热处理377
1 概述377
1.1 形变热处理的发展沿革377
1.4 形变热处理的方法分类378
2.1 低温形变热处理工艺379
2 低温形变热处理379
2.3 钢低温形变热处理后的力学性能383
2.2 钢低温形变热处理后的组织383
2.4 低温形变淬火强化机理389
3.1 工艺参数对高温形变淬火效果的影响391
3 高温形变热处理391
3.2 高温形变淬火钢的组织394
3.3 钢高温形变热处理后的力学性能396
3.4 高温形变淬火强化机理401
3.5 钢的锻热淬火402
3.6 控制轧制404
3.7 非调质钢405
4.1 形变诱发马氏体相变406
4 马氏体相变过程中的形变406
4.2 变塑现象和变塑钢407
5.1 马氏体形变强化的特点408
5 马氏体相变后的形变408
5.3 淬火马氏体的形变时效409
5.2 马氏体形变强化的原因409
5.4 回火马氏体的形变时效410
6.1 应力与形变对过冷奥氏体分解过程的影响411
6 形变与扩散型相变相结合的形变热处理411
5.5 大形变量的马氏体形变时效411
6.2 在扩散型相变前进行形变412
6.3 在扩散型相变中进行形变(等温形变淬火)414
6.4 在扩散型相变后进行形变416
7.1 利用强化效果遗传性的形变热处理418
7 其他形变热处理方法418
7.2 预先形变热处理419
7.3 多边化强化420
7.4 表面形变热处理421
7.5 形变化学热处理423
8.2 铜合金的形变热处理425
8.1 铝合金的形变热处理425
7.6 晶粒超细化处理425
7.7 复合形变热处理425
8 非铁金属的形变热处理425
1.2 低压气体放电426
1.1 等离子体426
第5章 等离子体热处理426
1 等离子体热处理基础426
2.1 等离子体化学热处理的基本原理431
2 等离子体化学热处理431
2.2 等离子体化学热处理设备434
2.3 等离子体化学热处理工艺435
3.1 等离子体物理气相沉积440
3 离子沉积技术440
3.2 等离子体化学气相沉积446
4.2 等离子体基离子注入技术的工作模式448
4.1 等离子体基离子注入技术的基本原理448
4 等离子体基离子注入技术448
4.4 离子注入技术改善表面性能的机理449
4.3 等离子体基离子注入技术的特点449
4.5 等离子体基离子注入技术的应用450
1.1 硬质涂层气相沉积技术的进展451
1 硬质涂层451
第6章 化学气相沉积和物理气相沉积451
1.3 硬质涂层对工业发展的贡献452
1.2 常用硬质涂层材料种类452
2.3 高温化学气相沉积技术453
2.2 化学气相沉积技术分类453
2 化学气相沉积453
2.1 化学气相沉积概述453
2.4 中温化学气相沉积(MT-CVD)技术460
2.5 低温化学气相沉积技术463
3.3 物理气相沉积的物理基础简介465
3.2 物理气相沉积分类465
3 物理气相沉积465
3.1 物理气相沉积概述465
3.4 各种物理气相沉积技术468
4.2 金刚石涂层的沉积技术482
4.1 非金属化合物超硬涂层种类482
4 非金属化合物超硬涂层气相沉积技术482
5.1 复合超硬涂层材料沉积技术的提出483
5 复合超硬涂层材料沉积技术483
4.3 立方氮化硼(CBN)涂层的沉积技术483
4.4 氮化碳(β-C3 N4)涂层沉积技术483
6.2 硬质涂层工具、模具应用举例484
6.1 硬质涂层的应用技术484
5.2 复合超硬涂层沉积技术484
6 硬质涂层工具、模具应用技术及举例484
7.1 硬质涂层的性能测试486
7 硬质涂层质量检测486
7.2 硬质涂层微观结构的测试487
参考文献490
第4篇 热处理设备495
2 热处理冷却设备497
1 热处理加热设备497
第1章 热处理设备分类497
4 热处理辅助设备498
3 热处理清洗和清理设备498
6 热处理环境保护设备499
5 热处理质量检测设备499
第2章 真空热处理设备500
1 气冷真空炉501
2 油冷真空炉504
4 多用途真空炉505
3 水冷真空炉505
8 真空烧结炉506
7 真空钎焊炉506
5 真空回火炉506
6 真空渗碳炉506
10 等离子热处理炉507
9 台车式真空炉507
2 普通型箱式电阻炉510
1 热处理电阻炉结构510
第3章 热处理电阻炉510
3 台车式电阻炉512
4 井式电阻炉513
5 钟罩式炉515
6 密封箱式炉516
8 推杆式炉518
7 转筒式炉518
9 输送带式炉及其生产线520
10 振底式炉522
13 滚筒式炉(鼓形炉)524
12 转底式炉524
11 辊底式炉524
15 牵引式炉525
14 步进式和摆动步进式炉525
16 自动化热处理设备526
1 浴炉的分类528
第4章 浴炉及流态粒子炉528
3 外部电加热中温浴炉529
2 低温浴炉529
4 燃料加热中温浴炉530
6 埋入式电极浴炉531
5 插入式电极盐浴炉531
7 流态粒子炉532
2 燃料炉炉型选择535
1 常用燃料炉分类535
第5章 热处理燃料炉535
3 燃料炉附属设备536
4 燃油烧嘴539
5 燃煤机541
6 预热器543
1 电子管式高频变频装置545
第6章 热处理感应加热及火焰加热装置545
3 晶体管(IGBT)式超音频变频装置546
2 晶体管式高频变频装置546
4 机式中频变频装置547
5 晶闸管式中频变频装置548
7 感应加热用热处理设备549
6 工频感应加热装置549
8 火焰表面加热装置552
1 激光表面热处理装置553
第7章 表面热处理设备553
3 气相沉积装置554
2 电子束表面改性装置554
2 淬火槽556
1 淬火冷却设备分类556
第8章 热处理冷却设备556
5 淬火介质冷却557
4 淬火槽加热装置557
3 淬火介质搅拌557
6 淬火槽输送机械558
9 冷处理设备559
8 淬火机床559
7 冷却过程的控制装置559
1.1 吸热式气氛发生装置561
1 可控气氛发生装置561
第9章 热处理辅助设备561
1.2 放热式气氛发生装置563
2 工业氮制备装置564
4 清洗设备566
3 氨分解气氛发生装置566
5 清理及强化设备568
6 矫直(校直)设备569
7 起重运输设备570
参考文献572
第5篇 材料热处理573
1.1 钢的分类及编号原则575
1 概述575
第1章 钢铁材料热处理575
1.2 常用合金元素577
2.2 渗碳钢584
2.1 低碳马氏体钢584
2 淬火低温回火合金结构钢及其热处理584
2.3 滚动轴承钢588
3.3 弹簧钢的品种590
3.2 成分特点590
3 弹簧钢及其热处理工艺590
3.1 性能要求590
3.5 特殊性能弹簧用钢和弹性合金591
3.4 热处理工艺591
4.4 调质钢零件的表面强化594
4.3 调质钢的热处理594
4 调质钢及其热处理工艺594
4.1 调质钢的性能要求594
4.2 调质钢的成分特点594
4.5 调质钢热处理技术的进展598
5.2 刃具用钢600
5.1 概述600
5 工具钢及其热处理工艺600
5.3 低合金刃具钢601
5.4 高速钢602
5.5 模具用钢606
6.1 不锈钢610
6 特殊钢及其热处理工艺610
6.2 耐热钢616
6.3 易切削钢和冷塑性成型用钢619
1.1 铝及铝合金622
1 铝及铝合金的热处理622
第2章 非铁金属的热处理622
1.2 变形铝合金的退火625
1.3 变形铝合金的固溶626
1.4 变形铝合金的时效627
1.6 变形铝合金加工及热处理状态标记630
1.5 变形铝合金的其他热处理630
1.7 铸造铝合金的热处理631
2.1 铜及铜合金633
2 铜及铜合金的热处理633
1.8 铝合金的热处理缺陷633
2.4 青铜的热处理638
2.3 黄铜的热处理638
2.2 工业纯铜的热处理638
3.1 钛及钛合金641
3 钛及钛合金的热处理641
2.5 白铜的热处理641
2.6 铜及铜合金热处理应注意的问题641
3.2 钛合金的退火644
3.5 钛合金热处理应注意的问题646
3.4 钛合金的形变热处理646
3.3 钛合金的固溶和时效646
4.1 镁及镁合金647
4 镁合金的热处理647
4.3 镁合金的固溶处理和时效648
4.2 镁合金的退火热处理648
5.1 镍和镍合金的热处理649
5 其他非铁金属的热处理649
5.2 钨、钼热处理650
1.2 铁基粉末冶金件的应用651
1.1 铁基粉末冶金材料的分类651
第3章 粉末冶金材料和零件的热处理651
1 铁基粉末冶金件的热处理651
1.3 铁基粉末冶金件的热处理653
2.1 钢结硬质合金的特点、牌号、性能和用途658
2 钢结硬质合金的热处理658
2.2 钢结硬质合金的热处理660
2.3 钢结碳质合金的组织与性能661
3.1 粉末高速钢类别和性能662
3 粉末高速钢的热处理662
4.1 硬质合金的分类和用途663
4 硬质合金的热处理663
3.2 热等静压和热挤压粉末高速钢663
4.2 硬质合金的热处理664
1.1 金属磁性的物理基础667
1 磁性合金的热处理667
第4章 功能合金的热处理667
1.2 软磁合金的热处理669
1.3 永磁合金的热处理680
2.1 金属的热膨胀特性692
2 膨胀合金的热处理692
2.2 低膨胀合金的热处理693
2.3 铁磁性定膨胀合金的热处理698
2.4 无磁性定膨胀合金的热处理704
2.5 高膨胀合金的热处理707
3.1 金属的弹性性能709
3 弹性合金的热处理709
3.2 高弹性合金的热处理711
3.3 恒弹性合金的热处理728
4.1 合金的超弹性和形状记忆效应734
4 形状记忆合金及其热处理734
4.2 钛镍形状记忆合金737
4.3 铜基形状记忆合金744
4.4 形状记忆合金的应用749
1.2 传质机理754
1.1 烧结驱动力754
第5章 陶瓷和硅酸盐材料的热处理754
1 陶瓷材料的烧结754
2.2 ZrO2陶瓷中的t-m相变755
2.1 ZrO2陶瓷中的c-t相变755
1.3 气氛对烧结的影响755
2 温度对陶瓷相变的影响755
3 熔体和玻璃体与温度的关系756
3.2 玻璃的形成757
3.1 熔体结构的形成757
1.1 铝基复合材料的强化热处理758
1 金属基复合材料的强化热处理758
第6章 复合材料的热处理758
1.2 镁合金基复合材料的强化热处理762
1.3 钛合金基复合材料的强化热处理763
2.1 概述766
2 金属基复合材料尺寸稳定化热处理766
2.2 铝合金基复合材料的冷热循环尺寸稳定化处理767
2.3 铝合金基复合材料的深冷尺寸稳定化处理768
参考文献770
第6篇 热处理CAD/CAM/CAE771
1.4 生产经验信息化处理773
1.3 热处理专家系统773
第1章 概述773
1 热处理计算机辅助工程分析和工艺编制773
1.1 知识重用773
1.2 热处理数据库773
4 热处理设备智能CAD技术774
3 热处理智能控制技术774
2 热处理数学建模与计算机模拟774
5.3 面向绿色制造的CAD/CAE技术775
5.2 产品制造全过程的CAE/CAPP775
4.1 热处理设备的知识重用技术775
4.2 热处理设备的科学计算775
4.3 热处理设备研究开发的决策系统775
5 热处理CAD/CAE/CAM与计算机集成制造775
5.1 轻量化高可靠产品的设计制造775
4 热处理计算机模拟技术的局限性776
3 热处理的数值模拟与实验研究的关系776
第2章 热处理计算机模拟的主要特点776
1 理论知识和定量科学计算直接应用于热处理生产776
2 计算机模拟使热处理向多学科交叉的综合性科学技术的方向发展776
3 有限差分法777
2 求解偏微分方程的方法777
第3章 热处理计算机模拟的基本方法777
1 描述热处理过程的偏微分方程777
4.1 单元划分779
4 用有限元法求解瞬态温度场779
4.2 用加权余值法进行有限元分析780
5.1 相变的计算782
5 瞬态温度场与相变的耦合782
4.3 三维瞬态导热的有限元分析782
5.4 相变超塑性784
5.3 应力对相变动力学的影响784
5.2 马氏体转变的计算784
6 界面换热系数的测定与计算785
1.2 热弹塑性本构关系787
1.1 热弹性本构方程787
第4章 热处理过程中应力场的数值计算787
1 热弹塑性应力场分析的基本原理787
1.4 组织转变对应力场的影响788
1.3 温度对应力场的影响788
1.5 热弹塑性应力场分析的主要算法789
2.2 热弹性有限元分析的方程790
2.1 虚功原理和最小位能原理790
2 热弹塑性应力场的有限元计算790
2.4 淬火应力场分析中总应变的处理791
2.3 热弹塑性应力应变关系791
3 淬火应力场的求解及边界条件792
2 流场动力学模拟793
1 化学热处理瞬态浓度场的数值模拟793
第5章 瞬态浓度场模拟与流场动力学模拟793
1.2 优化加热工艺的CAD技术795
1.1 三维温度场计算机模拟的实验验证795
第6章 应用实例795
1 阶梯轴加热CAE795
2 高硬冷轧辊淬火工艺CAE796
3 复杂形状零件淬火操作CAE/CAPP798
5 气体渗碳CAE/CAPP/CAM799
4 曲轴渗氮畸变控制CAE799
6 气体渗碳CAE/CAM800
8 热处理设备的智能CAD802
7 基于计算机模拟的动态可控渗氮技术802
参考文献804
第7篇 热处理清洁生产和安全805
1.5 电磁辐射807
1.4 废渣807
第1章 热处理的清洁生产807
1 热处理生产的污染源807
1.1 引起大气污染的主要根源807
1.2 对水质的污染807
1.3 噪声污染807
2 环境的控制和治理808
3.2 废水排放809
3.1 废气及烟尘排放809
3 热处理三废的排放809
4.2 JB/T 5073—1991规定的热处理车间空气中有害物质的最高允许浓度810
4.1 先进工业国家规定的空气中有害物质的限值810
3.3 固体废物810
4 空气中有害物质的限值810
5.1 国外情况811
5 热处理盐浴有害固体废物污染的管理811
5.2 JB/T 9052—1999关于热处理盐浴有害废弃物的规定812
6.2 盐浴固体废物及其毒性试验方法813
6.1 国内外情况813
6 热处理盐浴有害固体废物无害化处理方法813
6.3 盐浴废渣的无害化处理814
7.2 分析方法815
7.1 与本标准有关的国内外标准概况815
7 热处理盐浴有害固体废物的分析815
2.1 易燃物质817
2 热处理生产中的危险因素817
第2章 热处理的安全生产817
1 生产过程安全卫生的重要性817
2.2 易爆物质819
2.3 毒性物质820
2.4 高压电821
3.1 热辐射822
3 热处理生产中的有害因素822
2.5 炽热物体及腐蚀性物质822
2.6 致冷剂822
2.7 坠落物体或迸出物822
3.3 噪声823
3.2 电磁辐射823
3.5 有害气体824
3.4 粉尘824
5.1 生产物料826
5 生产物料和剩余物料826
4 热处理生产作业环境826
4.1 定义826
4.2 车间卫生826
4.3 作业场地空气中有害物质的最高允许浓度826
4.4 噪声控制826
4.5 照度标准及应急照明826
4.6 设备间的距离826
4.7 车间通道、安全标志和报警装置826
6.1 电阻炉827
6 生产装置827
5.2 剩余物料827
6.2 燃烧炉828
6.3 盐浴炉和流动粒子炉830
6.6 激光和电子束的热处理装置831
6.5 离子化学热处理设备831
6.4 感应加热装置831
6.8 火焰加热淬火装置832
6.7 淬火及回火油槽832
6.9 可控气氛的制备和可控气氛炉833
6.13 酸浸设备835
6.12 喷砂、喷丸和高压水清理设备835
6.10 冷处理设备835
6.11 清洗设备835
7.1 一般要求836
7 热处理工艺作业836
6.14 校直机836
6.15 炉用构件、料盘和夹具836
7.4 盐浴热处理837
7.3 化学热处理837
7.2 表面热处理837
8.1 基本要求838
8 安全、卫生防护技术措施838
7.5 真空热处理838
8.2 “四防”839
参考文献840
第8篇 热处理质量控制与无损检测841
2 热处理质量控制体系843
1 热处理质量管理的目的及主要内容843
第1章 热处理生产的质量管理843
4.2 工艺文件编制844
4.1 工艺试验844
3 产品设计中的热处理质量控制844
4 工艺设计中的质量控制844
5.2 零件材料的化学成分分析848
5.1 原材料控制的主要内容848
5 原材料质量控制848
1 热处理设备质量控制856
第2章 热处理工序的过程质量控制856
2 热处理质量检验控制859
4 热处理质量控制中常用的统计技术860
3 操作者技能和责任质量控制860
1.3 硫、磷元素的偏析862
1.2 低倍检验的一般方法862
第3章 热处理件的宏观和微观组织检验862
1 原材料缺陷的低倍检验862
1.1 常见的低倍缺陷特征862
2.3 常用的断口分析方法863
2.2 断口样品的切取和制备863
2 断口分析863
2.1 断口分析的用途863
2.4 典型断口形貌特征864
3.1 光学显微镜分析方法865
3 显微组织检验865
3.2 定量金相分析方法868
3.3 晶粒度测定方法870
3.5 电子显微镜分析方法872
3.4 高温和低温金相分析方法872
3.6 钢铁零件典型热处理显微组织与缺陷的金相特征873
1.1 布氏硬度875
1 硬度875
第4章 力学性能试验875
1.2 洛氏硬度877
1.3 维氏硬度和显微硬度878
1.5 硬度与强度及各种硬度之间的换算882
1.4 肖氏硬度和里氏硬度882
1.6 典型硬度计简介886
2.2 性能指标的计算888
2.1 试样888
2 拉伸888
4 弯曲889
3 压缩889
2.3 缺口拉伸与缺口偏拉伸889
2.4 高温拉伸和低温拉伸889
6 冲击890
5 扭转890
7 疲劳891
8 断裂韧度892
2 X射线法894
1 应力释放法894
第5章 残余应力测定894
5 深层应力分布测量896
4 超声波法896
3 磁性法896
1.1 磁化方法897
1 磁粉探伤897
第6章 热处理质量的无损检测方法897
1.2 磁化规范899
1.5 磁粉探伤的操作900
1.4 磁粉探伤设备900
1.3 磁粉与磁悬液900
1.6 磁痕分析901
2 涡流探伤902
3 渗透法探伤903
4.2 超声波探伤仪908
4.1 超声波探伤方法的种类908
4 超声波探伤908
4.4 探头909
4.3 试块909
4.5 检测910
5 X射线探伤912
5.1 X射线探伤设备913
5.2 X射线照相916
5.4 射线CT技术917
5.3 X射线电视探伤917
4 点腐蚀919
3 均匀腐蚀试验919
第7章 耐腐蚀性能测试919
1 工程上常见的腐蚀类型919
2 腐蚀速率评定方法919
5 晶间腐蚀920
8 大气腐蚀与高温氧化921
7 应力腐蚀开裂921
6 缝隙腐蚀921
参考文献923