图书介绍
汽车车身装焊夹具设计技术PDF|Epub|txt|kindle电子书版本网盘下载
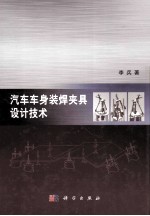
- 李兵著 著
- 出版社: 北京:科学出版社
- ISBN:9787030398994
- 出版时间:2014
- 标注页数:192页
- 文件大小:25MB
- 文件页数:201页
- 主题词:汽车-车体结构-焊接设备
PDF下载
下载说明
汽车车身装焊夹具设计技术PDF格式电子书版下载
下载的文件为RAR压缩包。需要使用解压软件进行解压得到PDF格式图书。建议使用BT下载工具Free Download Manager进行下载,简称FDM(免费,没有广告,支持多平台)。本站资源全部打包为BT种子。所以需要使用专业的BT下载软件进行下载。如BitComet qBittorrent uTorrent等BT下载工具。迅雷目前由于本站不是热门资源。不推荐使用!后期资源热门了。安装了迅雷也可以迅雷进行下载!
(文件页数 要大于 标注页数,上中下等多册电子书除外)
注意:本站所有压缩包均有解压码: 点击下载压缩包解压工具
图书目录
第1章 绪论1
1.1 引言1
1.2 汽车薄板件装配概述1
1.3 薄板接头型式与装配方式3
1.3.1 接头型式3
1.3.2 装配方式4
1.4 薄板装配定位及夹紧原理6
1.5 薄板件装配过程及其引入偏差7
1.5.1 薄板焊接步骤7
1.5.2 薄板偏差与关键特性8
1.5.3 薄板装配偏差源分析9
1.6 汽车薄板件装焊夹具设计研究现状11
1.6.1 柔性夹具及其设计方法研究现状12
1.6.2 柔性薄板件夹具设计理论研究现状14
1.7 本章小结15
参考文献15
第2章 汽车薄板件装配偏差建模与分析18
2.1 引言18
2.2 焊接偏差与点焊连接建模19
2.2.1 焊接偏差及回弹方程的建立19
2.2.2 点焊连接有限元模型20
2.3 定位偏差建模21
2.3.1 定位约束的数学描述21
2.3.2 定位偏差的螺旋模型23
2.4 夹紧偏差建模29
2.4.1 完全夹紧的数学模型29
2.4.2 夹紧偏差模型30
2.5 基于主成分分析的金属薄板变形分析33
2.5.1 误差源协方差矩阵的主成分分析34
2.5.2 基于PCA的金属薄板件装配变形分析35
2.5.3 稳健主成分分析36
2.5.4 实例分析37
2.6 基于小波的偏差源分析方法40
2.6.1 小波分析概述40
2.6.2 基于小波分析的薄板变形分解41
2.6.3 薄板焊接装配变形的仿真流程42
2.6.4 实例分析44
2.7 本章小结46
参考文献47
第3章 汽车薄板装配夹具布局稳健优化设计49
3.1 引言49
3.2 稳健设计概述49
3.3 基于遗传算法的薄板装配夹具布局稳健设计51
3.3.1 基于泰勒级数展开的优化设计模型51
3.3.2 基于遗传算法的稳健优化设计54
3.4 基于影响系数法的薄板装配稳健设计60
3.4.1 基于拉格朗日极值法的稳健指标60
3.4.2 薄板装配实例分析63
3.5 本章小结65
参考文献65
第4章 基于响应面法的夹具布局与装配公差优化67
4.1 引言67
4.2 响应面法及其近似建模67
4.3 基于稳健设计空间寻优的二阶段响应面法69
4.3.1 二阶段响应面法基本思想70
4.3.2 基于稳健设计空间搜索的改进响应面法优化流程图70
4.4 基于Kriging插值的改进响应面法71
4.4.1 Kriging估计量和关键参数71
4.4.2 基于Kriging插值的改进响应面法优化流程72
4.5 基于神经网络的改进响应面法73
4.5.1 BP神经网络模型74
4.5.2 基于神经网络的改进响应面法优化流程75
4.6 设计实例76
4.6.1 基于Kriging改进响应模型的薄板装配公差分配优化设计76
4.6.2 基于神经网络改进响应面法的夹具布局优化设计80
4.7 本章小结84
参考文献84
第5章 并联柔性夹具机构构型综合及可重构设计86
5.1 引言86
5.2 并联机器人机构研究现状86
5.2.1 并联机器人机构研究概述86
5.2.2 并联机构学理论研究的进展88
5.3 并联夹具系统总体设计方案及机构综合基础89
5.3.1 并联夹具系统的总体设计方案89
5.3.2 并联夹具机构综合理论基础90
5.4 一类三支路6-DOF并联机构构型综合92
5.4.1 机构综合流程92
5.4.2 机构支路构型枚举94
5.4.3 机构构型的构建96
5.5 并联机构构型的衍生机构设计99
5.5.1 位移流形等效法99
5.5.2 螺旋重构法100
5.6 并联夹具机构可重构设计103
5.6.1 并联夹具主体机构模块化设计104
5.6.2 并联夹具定位及夹紧单元模块设计105
5.7 新型并联柔性夹具系统集成106
5.8 本章小结107
参考文献108
第6章 并联柔性夹具机构运动学及设计空间建模111
6.1 引言111
6.2 并联夹具机构螺旋分析111
6.2.1 机构螺旋分析111
6.2.2 机构自由度确认113
6.2.3 驱动副有效性验证114
6.3 并联夹具机构位置逆解分析115
6.3.1 3-RUPR/UPS机构位置逆解115
6.3.2 3-UPU/UPS机构位置逆解118
6.3.3 3-UPU/UPU机构位置逆解119
6.4 并联夹具机构雅可比矩阵求解119
6.4.1 3-RUPR/UPS机构雅可比矩阵求解120
6.4.2 3-UPU/UPS机构雅可比矩阵求解121
6.4.3 3-UPU/UPU机构雅可比矩阵求解122
6.5 并联夹具机构参数设计空间建模122
6.5.1 3-RUPR/UPS并联夹具机构设计空间建模122
6.5.2 3-UPU/UPS及3-UPU/UPU并联夹具机构设计空间建模126
6.6 本章小结127
参考文献127
第7章 基于全域评价指标的并联柔性夹具机构性能分析129
7.1 引言129
7.2 并联夹具机构工作空间分析129
7.2.1 工作空间求解方法129
7.2.2 3-RUPR/UPS机构工作空间分析130
7.2.3 3-UPU/UPS机构及3-UPU/UPU机构工作空间分析133
7.3 并联夹具机构奇异性分析135
7.3.1 3-RUPR/UPS并联夹具机构的奇异性分析136
7.3.2 3-UPU/UPS及3-UPU/UPU并联夹具机构的奇异性分析137
7.3.3 并联夹具机构奇异性全域评价指标及奇异性分析138
7.4 并联夹具机构刚度性能分析142
7.4.1 机构全局刚度矩阵的建立143
7.4.2 支链变形分析及刚度建模144
7.4.3 并联夹具机构的刚度建模152
7.4.4 并联夹具机构刚度全域评价指标及刚度分析155
7.5 本章小结157
参考文献157
第8章 并联柔性夹具系统平台及实验研究159
8.1 引言159
8.2 并联夹具机构尺寸优化及样机设计159
8.2.1 并联夹具机构尺寸参数优化159
8.2.2 并联柔性装配夹具系统样机设计161
8.3 并联柔性装配夹具系统控制系统设计162
8.3.1 硬件系统162
8.3.2 软件系统165
8.4 并联柔性夹具机构实验研究167
8.5 本章小结171
参考文献172
附录173