图书介绍
焊工手册 埋弧焊·气体保护焊·电渣焊·等离子弧焊 第2版PDF|Epub|txt|kindle电子书版本网盘下载
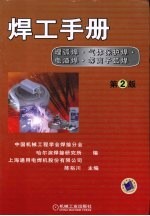
- 陈裕川主编 著
- 出版社: 北京:机械工业出版社
- ISBN:7111198468
- 出版时间:2007
- 标注页数:973页
- 文件大小:379MB
- 文件页数:1000页
- 主题词:焊接-技术手册
PDF下载
下载说明
焊工手册 埋弧焊·气体保护焊·电渣焊·等离子弧焊 第2版PDF格式电子书版下载
下载的文件为RAR压缩包。需要使用解压软件进行解压得到PDF格式图书。建议使用BT下载工具Free Download Manager进行下载,简称FDM(免费,没有广告,支持多平台)。本站资源全部打包为BT种子。所以需要使用专业的BT下载软件进行下载。如BitComet qBittorrent uTorrent等BT下载工具。迅雷目前由于本站不是热门资源。不推荐使用!后期资源热门了。安装了迅雷也可以迅雷进行下载!
(文件页数 要大于 标注页数,上中下等多册电子书除外)
注意:本站所有压缩包均有解压码: 点击下载压缩包解压工具
图书目录
第1篇 埋弧焊1
第1章 埋弧焊概论1
1.1 埋弧焊过程原理及其特点1
1.2 埋弧焊工艺方法及其分类2
1.2.1 单丝焊接法2
1.2.2 药芯焊丝焊接法4
1.2.3 加大焊丝伸出长度焊接法4
1.2.4 热丝埋弧焊接法5
1.2.5 添加冷丝埋弧焊接法5
1.2.6 多丝埋弧焊接法6
1.2.7 加金属粉末埋弧焊接法8
1.2.8 窄间隙埋弧焊9
1.3 埋弧焊的优缺点及适用范围10
1.3.1 埋弧焊的优缺点10
1.3.2 埋弧焊的适用范围10
第2章 埋弧焊用焊接材料12
2.1 埋弧焊的冶金特点12
2.2 埋弧焊时的主要冶金反应12
2.2.1 硅、锰还原反应12
2.2.2 碳的烧损13
2.2.3 去氢反应13
2.2.4 脱硫和脱磷反应13
2.3 埋弧焊用焊剂13
2.3.1 埋弧焊焊剂的分类13
2.3.2 对焊剂性能的基本要求14
2.3.3 埋弧焊焊剂的制造方法15
2.3.4 埋弧焊焊剂的标准型号和商品牌号17
2.3.5 焊剂的质量检验23
2.4 埋弧焊焊剂的选择27
2.4.1 碳钢埋弧焊焊剂的选择原则27
2.4.2 低合金钢埋弧焊焊剂的选择原则30
2.4.3 不锈钢埋弧焊焊剂的选择原则31
2.5 焊剂的储存与烘干31
2.6 埋弧焊用焊丝31
2.7 埋弧焊焊剂与焊丝的选配36
第3章 埋弧焊设备与工艺装备38
3.1 概述38
3.2 埋弧焊用焊接电源40
3.2.1 埋弧焊电源的种类及基本特性41
3.2.2 埋弧焊用整流电源44
3.2.3 埋弧焊电源的选用原则52
3.3 埋弧焊机的控制系统53
3.3.1 埋弧焊电弧的自动调节原理53
3.3.2 埋弧焊送丝系统控制电路55
3.3.3 埋弧焊机行走机构控制系统58
3.3.4 埋弧焊机的数控系统58
3.4 标准埋弧焊机和埋弧堆焊设备61
3.4.1 小车式埋弧焊机61
3.4.2 悬挂式埋弧焊机头68
3.5 埋弧焊焊接工艺装备77
3.5.1 焊接操作机77
3.5.2 焊件变位机械86
3.5.3 工装夹具94
3.5.4 组装机械105
第4章 埋弧焊工艺及技术108
4.1 埋弧焊工艺基础108
4.1.1 焊缝形成和结晶过程的一般规律108
4.1.2 焊接参数对焊缝成形的影响109
4.1.3 其他焊接参数对焊缝成形的影响111
4.2 埋弧焊接头的设计114
4.2.1 埋弧焊接头和坡口形式的设计原则114
4.2.2 埋弧焊接头坡口标准116
4.2.3 焊接衬垫120
4.3 埋弧焊焊前准备123
4.3.1 焊接坡口的制备123
4.3.2 焊材的准备124
4.3.3 焊件的组装124
4.4 埋弧焊操作技术125
4.4.1 引弧及收弧技术125
4.4.2 电弧长度的控制125
4.4.3 焊丝位置的调整126
4.4.4 焊道顺序的排列128
4.4.5 引弧板和引出板的设置130
4.5 埋弧焊工艺规程130
4.5.1 焊接工艺评定131
4.5.2 焊接参数的选择原则133
4.5.3 埋弧焊工艺的优化设计136
4.5.4 埋弧焊典型焊接参数136
第5章 碳素结构钢的埋弧焊工艺144
5.1 碳素结构钢的基本特性144
5.1.1 概述144
5.1.2 碳素结构钢的分类144
5.1.3 普通结构钢的基本特性144
5.1.4 优质碳素结构钢的基本特性146
5.1.5 特种用途碳素结构钢的基本特性147
5.2 碳素结构钢的焊接性及埋弧焊特点154
5.2.1 低碳钢的焊接性155
5.2.2 中碳钢的焊接性157
5.2.3 高碳钢的焊接性157
5.2.4 低碳钢埋弧焊工艺要点157
5.2.5 中碳钢埋弧焊工艺要点158
5.2.6 高碳钢埋弧焊工艺要点158
5.3 碳钢埋弧焊典型工艺规程158
5.3.1 20g中厚板对接接头的双面埋弧焊158
5.3.2 130mm中碳钢厚板加钢衬垫单V形坡口埋弧焊159
第6章 低合金结构钢埋弧焊工艺160
6.1 低合金结构钢的基本特性160
6.1.1 概述160
6.1.2 低合金结构钢的分类160
6.1.3 常用低合金结构钢的基本特性161
6.2 低合金结构钢的焊接性186
6.2.1 热影响区的组织变化186
6.2.2 冷裂纹敏感性187
6.2.3 接头的韧性187
6.2.4 再热裂纹敏感性188
6.2.5 热裂纹敏感性188
6.3 低合金结构钢的埋弧焊工艺190
6.3.1 焊前准备190
6.3.2 焊材选择193
6.3.3 焊接工艺方案208
6.3.4 焊接工艺参数208
6.3.5 操作技术209
6.3.6 焊后热处理209
6.4 常用低合金钢埋弧焊工艺及接头典型的性能212
6.4.1 Q345(16Mn,16MnR)钢的埋弧焊212
6.4.2 Q390(15MnV,15MnVR)钢的埋弧焊213
6.4.3 13MnNiMoNbR钢的厚板埋弧焊214
6.4.4 15MnMoVN调质高强钢的埋弧焊215
6.4.5 15CrMo(15CrMoR)低合金耐热钢的埋弧焊216
6.4.6 12Cr1MoV低合金耐热钢的埋弧焊216
6.4.7 12Cr2Mo1(12Cr2Mo1R)低合金耐热钢的埋弧焊219
6.4.8 22NiMoCr37核容器用钢的埋弧焊219
6.4.9 低温用3.5Ni钢的埋弧焊221
第7章 中合金钢埋弧焊工艺223
7.1 中合金结构钢的基本特性223
7.1.1 中合金耐热钢223
7.1.2 中合金低温钢224
7.2 中合金结构钢的焊接性226
7.2.1 中合金耐热钢的焊接性226
7.2.2 中合金低温镍钢的焊接性228
7.3 中合金钢的埋弧焊工艺229
7.3.1 中合金耐热钢的埋弧焊工艺229
7.3.2 中合金低温镍钢的埋弧焊工艺233
7.4 常用中合金钢埋弧焊工艺及接头典型的性能235
7.4.1 常用中合金耐热钢的焊接工艺规程235
7.4.2 常用中合金低温镍钢的焊接工艺规程236
第8章 高合金结构钢的埋弧焊工艺240
8.1 高合金结构钢的基本特性240
8.1.1 概述240
8.1.2 高合金不锈钢240
8.1.3 高合金耐热钢252
8.2 高合金结构钢的焊接性258
8.2.1 高合金结构钢的金相组织258
8.2.2 高合金不锈钢的焊接性259
8.3 高合金结构钢的埋弧焊工艺261
8.3.1 铁素体不锈钢的埋弧焊工艺261
8.3.2 奥氏体不锈钢的焊接性及埋弧焊特点264
8.3.3 高合金耐热钢的焊接性及埋弧焊工艺279
第9章 埋弧焊接头中的常见缺陷及其防治方法289
9.1 埋弧焊接头中常见缺陷的种类和形貌289
9.1.1 裂纹的种类和形貌289
9.1.2 未焊透和未熔合的典型形貌292
9.1.3 气孔的形貌292
9.1.4 夹渣的形貌292
9.1.5 咬边、焊瘤和溢流的形貌292
9.2 埋弧焊接头中缺陷形成的原因294
9.3 缺陷的防止措施298
9.4 焊接缺陷的清除和修补306
9.4.1 焊接缺陷的清除306
9.4.2 焊接缺陷的修补306
第10章 埋弧堆焊307
10.1 埋弧堆焊方法307
10.1.1 概述307
10.1.2 埋弧堆焊方法原理308
10.1.3 高效埋弧堆焊法312
10.1.4 埋弧堆焊方法的选择316
10.2 带极埋弧堆焊的冶金和工艺特点317
10.2.1 带极熔化特点317
10.2.2 堆焊金属的渗合金319
10.2.3 带极堆焊时母材的熔化特点320
10.2.4 带极堆焊的效率323
10.3 埋弧堆焊用焊接材料325
10.3.1 堆焊材料的分类325
10.3.2 带极埋弧堆焊材料326
10.4 埋弧堆焊工艺329
10.4.1 埋弧堆焊工艺要点329
10.4.2 堆焊层的焊后加工及热处理331
10.4.3 堆焊操作技术332
10.5 各种材料的带极埋弧堆焊工艺333
10.5.1 碳钢带极堆焊工艺333
10.5.2 耐蚀合金的堆焊工艺333
10.5.3 耐磨合金的堆焊工艺336
10.5.4 有色金属的堆焊336
第11章 埋弧焊生产应用实例337
11.1 实例1 5万kW高压加热器壳体纵缝双面埋弧焊337
11.1.1 概述337
11.1.2 焊接工艺337
11.1.3 接头性能338
11.2 实例2 20MPa蓄势器筒体环缝埋弧焊338
11.2.1 概述338
11.2.2 焊接工艺339
11.2.3 焊后检查339
11.2.4 接头性能339
11.3 实例3 疏水冷却器纵环缝埋弧焊339
11.3.1 概述339
11.3.2 焊接工艺340
11.3.3 焊后检查341
11.3.4 接头性能341
11.4 实例4 600MW锅炉梁柱角接缝及腹板拼接埋弧焊341
11.4.1 概述341
11.4.2 腹板拼接焊341
11.4.3 梁与柱角接缝埋弧焊342
11.5 实例5 600MW锅炉锅筒纵环缝窄间隙埋弧焊343
11.5.1 概述343
11.5.2 锅筒纵环缝焊接工艺344
11.5.3 焊后检查345
11.5.4 接头性能345
11.6 实例6 铁路桥梁构件的埋弧焊345
11.6.1 九江长江大桥概况345
11.6.2 杆件埋弧焊工艺346
11.6.3 埋弧焊接头典型力学性能348
11.6.4 焊接接头的无损检验348
11.7 实例7 CO2汽提塔球形封头与下筒体及凸缘间接缝的埋弧焊349
11.7.1 概述349
11.7.2 焊前准备350
11.7.3 焊接工艺350
11.7.4 BHW-35(13MnNiMo54)对接接头性能350
11.7.5 BHW-35与20MnMo锻件对接埋弧焊351
11.8 实例8 200MW电站锅炉锅筒纵环缝窄间隙埋弧焊351
11.8.1 概述351
11.8.2 纵环缝窄间隙埋弧焊工艺352
11.8.3 焊后检查353
11.8.4 接头性能353
11.9 实例9 高压球形气瓶环缝埋弧焊353
11.9.1 概述353
11.9.2 环缝埋弧焊工艺354
11.9.3 焊后检查355
11.9.4 接头典型力学性能355
11.10 实例10 300MW电站锅炉铬钼耐热钢集箱环缝埋弧焊355
11.10.1 概述355
11.10.2 焊接工艺355
11.10.3 焊后检查356
11.10.4 接头性能356
11.11 实例11 汽化炉壳体纵环缝的窄间隙埋弧焊357
11.11.1 概述357
11.11.2 焊接工艺357
11.11.3 焊后检查358
11.11.4 接头性能358
11.12 实例12 80万t/a加氢反应器环缝埋弧焊358
11.12.1 概述358
11.12.2 焊接工艺358
11.12.3 焊后检查359
11.12.4 接头力学性能359
11.13 实例13 600MW电站锅炉过热器集箱环缝埋弧焊360
11.13.1 概述360
11.13.2 焊接工艺360
11.13.3 焊后检查361
11.13.4 接头力学性能361
11.14 实例14 9%Ni钢液化天然气大型储罐环缝埋弧焊361
11.14.1 概述361
11.14.2 焊接工艺362
11.14.3 焊后检查363
11.14.4 接头的力学性能363
11.15 实例15 1Cr18Ni9Ti不锈钢板对接埋弧焊363
11.15.1 概述363
11.15.2 焊接工艺364
11.15.3 接头各项性能364
11.16 实例16 300MW电站锅炉高压加热器管板带极堆焊364
11.16.1 概述364
11.16.2 堆焊工艺364
11.16.3 焊后检查及接头力学性能365
11.17 实例17 24万t/a尿素装置汽提塔管板带极埋弧堆焊365
11.17.1 概述365
11.17.2 堆焊工艺365
11.17.3 焊后检查365
11.18 实例18 300MW混流式水轮机转轮双金属上冠不锈钢带极埋弧堆焊366
11.18.1 概述366
11.18.2 堆焊工艺及试验结果366
11.19 实例19 水泥挤压辊药芯带极埋弧堆焊367
11.19.1 概述367
11.19.2 堆焊工艺及检查结果367
11.20 实例20 热轧工作辊丝极埋弧堆焊368
11.20.1 概述368
11.20.2 堆焊材料的选择368
11.20.3 堆焊工艺369
11.20.4 堆焊层的检查369
11.20.5 硬度检测370
参考文献370
第2篇 气体保护电弧焊371
第12章 气体保护电弧焊方法概论371
12.1 气体保护电弧焊原理371
12.2 气体保护焊的分类371
12.2.1 熔化极气体保护焊372
12.2.2 非熔化极气体保护焊373
12.3 新型气体保护焊方法简介373
12.3.1 双丝气体保护焊373
12.3.2 表面张力过渡CO2焊374
12.3.3 热丝TIG焊375
12.3.4 活性助焊剂-TIG焊375
12.3.5 气电立焊376
12.3.6 电弧定位焊377
12.3.7 窄间隙焊接377
12.4 气体保护焊的冶金特点378
12.4.1 氧化还原反应378
12.4.2 硅、锰脱氧反应378
12.5 熔滴过渡特性379
12.6 熔透特性381
12.7 气体保护焊的优缺点及应用范围383
12.7.1 气体保护焊的优缺点383
12.7.2 气体保护焊的应用范围383
第13章 气体保护焊用焊接材料385
13.1 气体保护焊用保护气体385
13.1.1 保护气体的种类及应用范围385
13.1.2 保护气体的选用原则387
13.1.3 保护气体标准389
13.2 气体保护焊用焊丝390
13.2.1 碳钢及低合金钢焊丝391
13.2.2 不锈钢焊丝397
13.2.3 铝及铝合金焊丝401
13.2.4 铜及铜合金焊丝410
13.2.5 镍及镍合金焊丝414
13.2.6 钛及钛合金焊丝414
13.2.7 碳钢药芯焊丝417
13.2.8 低合金钢药芯焊丝422
13.2.9 不锈钢药芯焊丝424
13.2.10 药芯焊丝牌号的表示方法430
13.3 焊丝的选用431
13.3.1 焊丝选用的基本要点431
13.3.2 碳钢和低合金高强钢焊丝的选用433
13.3.3 耐热钢用焊丝的选用436
13.3.4 低温钢用焊丝的选用436
13.3.5 耐候钢用焊丝的选用439
13.3.6 不锈钢及异种钢用焊丝的选用439
13.4 气体保护焊用钨极443
13.4.1 钨极的分类443
13.4.2 钨极的尖端形状及选用444
第14章 气体保护焊设备及工艺装备447
14.1 概述447
14.2 熔化极气体保护焊设备447
14.2.1 设备的基本构成447
14.2.2 焊接电源447
14.2.3 送丝系统462
14.2.4 气路系统471
14.2.5 水路系统478
14.2.6 焊枪478
14.2.7 控制系统482
14.2.8 熔化极气体保护焊设备技术特性数据484
14.3 非熔化极气体保护焊设备495
14.3.1 非熔化极气体保护焊设备的基本构成495
14.3.2 焊接电源495
14.3.3 高频振荡器501
14.3.4 高压脉冲发生器501
14.3.5 电流衰减装置502
14.3.6 焊枪503
14.3.7 通用非熔化极气体保护焊设备性能504
14.3.8 自动TIG焊设备506
14.4 气体保护焊工艺装备530
14.4.1 气体保护焊焊接操作机530
14.4.2 气体保护焊用焊件变位机械535
14.4.3 气体保护焊用工装夹具535
14.5 弧焊机器人系统537
14.6 气体保护焊设备的选用543
14.6.1 半自动焊设备的选用543
14.6.2 自动焊设备的选用543
14.7 气体保护焊设备的常见故障及维护544
第15章 二氧化碳和混合气体保护焊工艺546
15.1 二氧化碳气体保护焊546
15.1.1 CO2气体保护焊参数及其影响因素546
15.1.2 坡口形状设计与焊接参数选择550
15.1.3 焊前准备550
15.1.4 焊接技术562
15.1.5 CO2堆焊与焊接修复573
15.2 混合气体保护焊(MAG焊)575
15.2.1 MAG焊的基本特点575
15.2.2 保护气体成分对MAG焊过程的影响576
15.2.3 MAG焊常用的焊接参数577
15.3 气电立焊与电弧点焊582
15.3.1 气电立焊的接头形式与焊接参数582
15.3.2 电弧点焊的接头形式与焊接参数583
第16章 熔化极惰性气体保护焊工艺586
16.1 铝及铝合金的MIG焊586
16.1.1 铝及铝合金的类型及型号表示方法586
16.1.2 铝及铝合金的规格及特性587
16.1.3 铝及铝合金的焊接特点593
16.1.4 焊前准备593
16.1.5 焊接参数的选择594
16.1.6 焊接操作技术608
16.2 铜及铜合金的MIG焊615
16.2.1 铜及铜合金的类型及型号表示方法615
16.2.2 铜及铜合金的规格和焊接特点616
16.2.3 焊接材料的选用626
16.2.4 焊接参数的选择627
16.3 镍及镍合金的MIG焊633
16.3.1 镍及镍合金的类型、特性及型号表示方法633
16.3.2 镍及镍合金的规格和焊接特点634
16.3.3 焊前准备635
16.3.4 焊接参数的选择与焊接技术638
16.4 钛及钛合金的MIG焊640
16.4.1 钛及钛合金的类型、特性及型号表示方法640
16.4.2 钛及钛合金的规格和焊接特点641
16.4.3 坡口形式设计与焊前准备644
16.4.4 焊接参数的选择645
16.5 镁及镁合金的MIG焊647
16.5.1 镁及镁合金的类型、特性及型号表示方法647
16.5.2 镁及镁合金的成分和焊接特点647
16.5.3 坡口形式设计与焊前准备649
16.5.4 焊接参数的选择651
16.6 不锈钢的MIG焊656
第17章 熔化极气体保护焊应用实例661
17.1 CO2气体保护焊应用实例661
17.1.1 在汽车制造业的应用661
17.1.2 在机车车辆制造业的应用663
17.1.3 在造船业的应用665
17.1.4 在起重机制造业的应用670
17.1.5 在摩托车制造业的应用672
17.1.6 在锅炉/压力容器制造业的应用674
17.1.7 在重型机电设备制造业的应用676
17.1.8 在轻工机械制造业的应用680
17.1.9 在建筑业的应用683
17.1.10 在焊接修复中的应用684
17.2 MAG焊应用实例687
17.2.1 汽车车轮的双枪自动MAG焊687
17.2.2 贮液罐阀体的MAG焊689
17.2.3 加氢高压空冷器深小孔内角缝MAG焊691
17.2.4 钢板组合件的自动MAG焊692
17.2.5 集装箱波纹板的自动MAG焊693
17.2.6 锅炉膜式水冷壁的脉冲MAG焊694
17.2.7 异种钢转矩拉杆的MAG焊696
17.2.8 货车储气缸纵缝MAG焊696
17.2.9 筒体环缝的MAG焊697
17.2.10 小球容器改进型环向对接接头MAG焊699
17.2.11 电动机端板的MAG电弧定位焊700
17.2.12 提升机底座的MAG焊701
17.2.13 飞机前轮连杆的MAG焊702
17.3 MIG焊应用实例703
17.3.1 铝储罐的半自动MIG焊703
17.3.2 铝型材散热器与导电排的自动MIG焊704
17.3.3 铝合金管道的自动MIG焊705
17.3.4 铝合金压力罐的三焊枪自动MIG焊706
17.3.5 铜镍合金管对接接头的自动MIG焊707
17.3.6 高炉纯铜螺旋风口的自动MIG焊708
17.3.7 低碳Mn-Mo钢筒体内表面MIG堆焊709
17.3.8 换热器用半圆管的自动MIG焊709
17.3.9 大厚度铝母线的半自动MIG焊710
第18章 钨极惰性气体保护焊工艺712
18.1 TIG焊的基本特点及应用范围712
18.1.1 TIG焊的基本特点712
18.1.2 TIG焊的应用范围712
18.2 TIG焊工艺方法712
18.2.1 直流TIG焊712
18.2.2 交流TIG焊713
18.2.3 脉冲TIG焊714
18.2.4 热丝TIG焊716
18.2.5 TIG电弧定位焊716
18.3 TIG焊技术718
18.3.1 接头形式718
18.3.2 焊前清理719
18.3.3 电源种类及极性720
18.3.4 保护气体和钨极721
18.3.5 焊接操作技术722
18.4 各种材料的TIG焊工艺729
18.4.1 铝及铝合金的TIG焊工艺729
18.4.2 铜及铜合金的TIG焊工艺737
18.4.3 镍及镍合金的TIG焊工艺744
18.4.4 钛及钛合金的TIG焊工艺746
18.4.5 镁及镁合金的TIG焊工艺747
18.4.6 各种钢材的TIG焊工艺749
18.5 TIG焊应用实例752
18.5.1 省煤器管的分段控制自动TIG焊752
18.5.2 薄板对接脉冲TIG焊753
18.5.3 加氢空冷器管箱与换热管接头的TIG焊754
18.5.4 转椅支腿的自动TIG焊756
18.5.5 拖拉机发动机罩的自动TIG焊757
18.5.6 宇航大型铝合金贮箱箱底的机器人TIG焊758
18.5.7 不锈钢波纹管的TIG焊759
18.5.8 陶瓷墙地砖模具的TIG焊修复759
18.5.9 空分装置铝合金的二人双面同步TIG焊760
18.5.10 不锈钢筛网的TIG焊760
18.5.11 锡青铜古钟的TIG焊修复761
18.5.12 纯铜厚大件的氩氮混合气体保护TIG焊762
第19章 药芯焊丝电弧焊764
19.1 药芯焊丝电弧焊的工作原理764
19.2 药芯焊丝电弧焊的冶金特性765
19.3 药芯焊丝电弧焊的优缺点与应用范围765
19.3.1 药芯焊丝电弧焊的优缺点765
19.3.2 药芯焊丝电弧焊的应用范围767
19.4 焊接材料767
19.4.1 保护气体767
19.4.2 药芯焊丝的分类768
19.4.3 碳钢和低合金钢药芯焊丝769
19.4.4 不锈钢药芯焊丝773
19.4.5 堆焊用药芯焊丝774
19.5 焊接设备777
19.5.1 焊枪777
19.5.2 送丝机构777
19.6 药芯焊丝电弧焊焊接工艺778
19.6.1 平焊作业778
19.6.2 横焊作业780
19.6.3 立焊作业780
19.6.4 仰焊作业782
19.7 药芯焊丝气电立焊782
19.7.1 气电立焊的优点782
19.7.2 气电立焊设备783
19.7.3 气电立焊焊接工艺783
19.8 药芯焊丝电弧点焊786
19.8.1 应用范围及特点786
19.8.2 工艺参数786
19.9 药芯焊丝电弧焊工艺参数举例787
19.10 药芯焊丝电弧焊应用实例791
19.10.1 异种钢齿轮的焊接791
19.10.2 2×20MN油压机工作台的焊接793
19.10.3 水轮机部件的堆焊793
19.10.4 液化石油气铁道罐车的焊接795
19.10.5 潜水电机壳体的双头CO2气体保护焊796
19.10.6 大型原油储罐的气电立焊797
19.10.7 提高熔敷速度并增加熔透尺寸的实例798
19.10.8 槽钢拼成方形构件的自动药芯电弧焊799
第20章 气体保护焊常见缺陷及其防止措施801
20.1 焊接缺陷的成因801
20.1.1 送丝不稳801
20.1.2 电弧电压(弧长)波动801
20.1.3 焊接飞溅大802
20.1.4 磁偏吹802
20.1.5 TIG焊时焊接工艺不合理802
20.2 熔化极气体保护焊缺陷及其防止措施802
20.2.1 焊缝外形缺陷803
20.2.2 气孔805
20.2.3 夹渣806
20.2.4 裂纹806
20.3 TIG焊缺陷及对策807
20.4 有色金属焊接缺陷及对策808
20.4.1 铝及铝合金焊接缺陷808
20.4.2 铜及铜合金焊接缺陷809
20.4.3 镍及镍合金焊接缺陷810
20.4.4 钛及钛合金焊接缺陷810
20.4.5 镁及镁合金焊接缺陷810
参考文献811
第3篇 电渣焊814
第21章 电渣焊方法概论814
21.1 电渣焊过程原理及其特点814
21.2 电渣焊的特点814
21.3 电渣焊接法的分类及应用范围815
21.3.1 电渣焊接法的分类815
21.3.2 电渣焊的应用范围816
第22章 电渣焊过程的冶金及结晶特点819
22.1 电渣焊过程的冶金特点819
22.2 电渣焊过程中金属的氧化和还原反应819
22.3 脱硫、脱磷反应821
22.3.1 脱硫反应821
22.3.2 脱磷反应821
22.4 焊缝金属中的氢和氮821
22.5 焊缝金属中的非金属夹杂物822
22.6 电渣焊焊缝金属的结晶822
22.6.1 电渣焊的热源822
22.6.2 金属熔池的结晶823
22.7 电渣焊接头的热影响区组织824
第23章 电渣焊的焊接材料825
23.1 电渣焊用焊剂825
23.1.1 焊剂的作用825
23.1.2 对电渣焊用焊剂的要求825
23.1.3 焊剂的碱度826
23.1.4 电渣焊用焊剂的选择826
23.2 电渣焊用电极材料828
23.2.1 对电渣焊用电极材料的要求828
23.2.2 电渣焊用电极材料标准829
23.2.3 电渣焊电极材料的选用830
第24章 电渣焊设备及其工艺装备832
24.1 电渣焊设备的组成及分类832
24.1.1 电渣焊设备的组成832
24.1.2 电渣焊设备的分类832
24.2 丝极电渣焊设备832
24.2.1 丝极电渣焊设备的执行机构832
24.2.2 纵缝丝极电渣焊机及其工艺装备832
24.2.3 环缝丝极电渣焊机及其工艺装备838
24.2.4 多功能电渣焊机840
24.3 板极电渣焊设备841
24.3.1 板极电渣焊机的特点841
24.3.2 板极电渣焊机的执行机构841
24.4 熔嘴电渣焊机841
24.4.1 熔嘴电渣焊机的特点841
24.4.2 熔嘴电渣焊机的执行机构841
24.4.3 熔嘴电渣焊机的类别841
24.5 接触电渣焊机842
24.5.1 接触电渣焊机的特点842
24.5.2 接触电渣焊机的执行机构842
24.5.3 国产HDS系列电渣压力焊设备的性能842
24.6 电渣焊用焊接电源843
24.7 丝极电渣焊机的控制系统845
24.8 带极电渣堆焊机846
第25章 电渣焊工艺及技术849
25.1 电渣焊焊接工艺基础849
25.1.1 接头形式的设计849
25.1.2 焊前准备850
25.1.3 接缝的装配850
25.2 电渣焊参数851
25.2.1 焊接参数的影响851
25.2.2 焊接参数的选择853
25.2.3 典型的电渣焊参数857
25.3 电渣焊操作技术861
25.3.1 焊接器材的准备861
25.3.2 焊前检查862
25.3.3 直缝丝极电渣焊操作技术862
25.3.4 环缝丝极电渣焊的操作技术863
25.3.5 板状熔嘴电渣焊操作技术865
25.3.6 管状熔嘴电渣焊操作技术865
25.3.7 板极电渣焊操作技术866
25.4 特种电渣焊工艺866
25.4.1 接触电渣焊工艺866
25.4.2 电渣带极堆焊工艺867
第26章 各种钢材的电渣焊工艺869
26.1 碳素钢的电渣焊工艺869
26.1.1 低碳钢的电渣焊工艺869
26.1.2 中碳钢的电渣焊工艺869
26.2 低合金高强度钢的电渣焊工艺870
26.2.1 低合金高强度钢电渣焊的特点870
26.2.2 16Mn钢的电渣焊工艺870
26.2.3 15MnV钢的电渣焊工艺871
26.2.4 15MnTi钢的电渣焊工艺871
26.2.5 19Mn6钢的电渣焊工艺871
26.2.6 18MnMoNb钢的电渣焊工艺871
26.2.7 13MnNiMo54钢的电渣焊工艺872
26.3 低合金高强度钢电渣焊的典型工艺参数872
26.4 低合金耐热钢的电渣焊工艺872
26.4.1 低合金耐热钢电渣焊的特点872
26.4.2 12CrMo钢的电渣焊工艺873
26.4.3 15CrMo钢的电渣焊工艺873
26.4.4 12Cr2Mo钢的电渣焊工艺873
26.4.5 低合金耐热钢电渣焊的典型工艺参数873
26.5 奥氏体不锈钢的电渣焊工艺873
26.5.1 奥氏体不锈钢电渣焊的特点874
26.5.2 奥氏体不锈钢电渣焊用焊接材料874
26.5.3 奥氏体不锈钢电渣焊接头的焊后热处理874
26.5.4 奥氏体不锈钢电渣焊的典型工艺参数及接头的性能874
26.6 奥氏体不锈钢带极电渣堆焊工艺875
26.6.1 不锈钢覆层堆焊的特点875
26.6.2 电渣堆焊的优点876
26.6.3 奥氏体不锈钢带极电渣堆焊的工艺要点876
第27章 电渣焊接头的常见缺陷及其防治方法879
27.1 电渣焊接头中常见缺陷的种类和形貌879
27.1.1 裂纹879
27.1.2 夹渣880
27.1.3 气孔880
27.1.4 未熔合881
27.2 电渣焊接头中缺陷形成的原因881
27.2.1 裂纹形成的原因881
27.2.2 夹渣形成的原因883
27.2.3 气孔形成的原因883
27.2.4 未熔合形成的原因883
27.3 电渣焊接头缺陷的防治方法884
27.3.1 电渣焊接头中裂纹的防治方法884
27.3.2 夹渣和未熔合的防治方法885
27.3.3 气孔的防治方法886
27.4 焊接缺陷的清除和修补886
27.4.1 焊接缺陷的清除886
27.4.2 焊接缺陷的修补886
第28章 电渣焊的应用实例887
28.1 实例1 电站锅炉锅筒纵缝丝极电渣焊887
28.1.1 锅筒结构简介887
28.1.2 筒体纵缝的丝极电渣焊888
28.1.3 筒体电渣焊纵缝和接头的理化性能及质量检验889
28.2 实例2 325MW水轮发电机主轴丝极环缝电渣焊889
28.2.1 焊件简图889
28.2.2 焊前装配889
28.2.3 焊接工艺890
28.2.4 产品试板检验结果891
28.3 实例3 27000DWT货轮艉柱电渣焊892
28.3.1 部件结构简介892
28.3.2 焊接设备、材料及接头设计892
28.3.3 焊前准备892
28.3.4 焊接及焊后热处理893
28.3.5 焊接接头检验894
28.4 实例4 大直径厚壁椭圆封头瓦瓣片的电渣焊894
28.4.1 部件结构简介894
28.4.2 变位器及冷却垫板894
28.4.3 焊接工艺895
28.5 实例5 3000t汽车纵梁油压机电渣焊896
28.5.1 产品结构简介896
28.5.2 焊前准备896
28.5.3 装配897
28.5.4 焊接897
28.5.5 焊后热处理897
28.6 实例6 高压容器纵缝熔嘴电渣焊898
28.6.1 产品结构简介898
28.6.2 焊接设备及工装898
28.6.3 焊接材料898
28.6.4 电渣焊接工艺898
28.6.5 焊缝质量检验899
28.7 实例7 1200型冷轧机机架电渣焊899
28.7.1 机架结构简介899
28.7.2 焊接设备及焊接材料899
28.7.3 机架装配及焊前准备899
28.7.4 机架的焊接900
28.7.5 焊后热处理900
28.7.6 焊缝质量检验900
28.8 实例8 发汗罐管板拼缝的管状熔嘴电渣焊901
28.8.1 焊接设备及电源901
28.8.2 管状熔嘴制造901
28.8.3 装配和焊接901
28.8.4 焊接接头的力学性能902
28.9 实例9 水轮发电机座环的电渣焊902
28.9.1 座环简介902
28.9.2 座环装配903
28.9.3 座环焊接903
28.9.4 座环电渣焊焊缝焊后探伤及热处理904
28.10 实例10 建筑结构箱形梁隔板与侧板接头的管状熔嘴电渣焊904
28.10.1 箱形梁结构简介904
28.10.2 组装与焊前准备904
28.10.3 焊接材料904
28.10.4 焊接设备904
28.10.5 焊接参数904
28.10.6 焊后检查904
28.11 实例11 公路桥伸缩梁拼接缝的窄坡口管状熔嘴电渣焊905
28.11.1 接头形式简介905
28.11.2 焊接设备与焊接材料905
28.11.3 焊接参数905
28.11.4 焊接接头力学性能检验结果905
28.12 实例12 加氢反应器不锈钢带极电渣堆焊905
28.12.1 概述905
28.12.2 不锈钢堆焊层的主要设计指标906
28.12.3 产品堆焊工艺及检验906
参考文献907
第4篇 等离子弧焊908
第29章 等离子弧焊方法908
29.1 概述908
29.2 等离子弧焊的原理909
29.3 等离子弧焊方法分类910
29.3.1 等离子弧类型910
29.3.2 等离子弧焊方法的分类910
29.4 等离子弧焊的优点912
29.5 等离子弧焊的应用范围913
29.5.1 适用的结构材料913
29.5.2 适用的厚度范围及接头形式913
第30章 等离子弧焊设备914
30.1 等离子弧焊设备的构成914
30.2 等离子弧焊用焊接电源915
30.3 等离子弧焊机的控制系统916
30.4 等离子弧焊枪921
30.4.1 喷嘴921
30.4.2 上枪体和下枪体922
第31章 等离子弧焊工艺925
31.1 概述925
31.2 焊接参数的影响925
31.2.1 焊接电流的影响925
31.2.2 焊接速度的影响926
31.2.3 离子气流量的影响926
31.2.4 钨极内缩长度的影响927
31.2.5 喷嘴距离的影响927
31.2.6 保护气体流量的影响927
31.2.7 其他焊接参数928
31.3 等离子弧焊的接头形式929
31.4 等离子弧焊的焊前准备929
31.4.1 焊件接缝的组装929
31.4.2 焊前清理930
31.4.3 钨极的准备931
31.5 等离子弧焊典型焊接参数931
31.5.1 微束等离子弧焊典型焊接参数931
31.5.2 熔透型等离子弧焊典型参数931
31.5.3 锁孔型等离子弧焊典型参数932
第32章 各种金属材料的等离子弧焊工艺935
32.1 碳钢及低合金钢的等离子弧焊工艺935
32.2 不锈钢的等离子弧焊工艺936
32.3 铜及铜合金的等离子弧焊工艺937
32.4 铝及铝合金的等离子弧焊工艺938
32.5 钛及其合金的等离子弧焊工艺940
第33章 等离子弧焊的常见缺陷及其防止方法942
33.1 等离子弧焊接头中常见缺陷的种类942
33.2 等离子弧焊接头中缺陷形成的原因942
33.3 等离子弧堆焊层中缺陷形成的原因943
33.4 焊接缺陷的防止措施943
33.4.1 等离子弧焊接头缺陷的防止措施943
33.4.2 等离子弧堆焊层中缺陷的防止措施945
第34章 等离子弧堆焊946
34.1 等离子弧堆焊原理及分类946
34.2 填丝等离子弧堆焊947
34.2.1 冷丝等离子弧堆焊947
34.2.2 热丝等离子弧堆焊947
34.3 粉末等离子弧堆焊(喷焊)950
34.3.1 粉末等离子弧堆焊的特点950
34.3.2 粉末等离子弧堆焊设备951
34.3.3 堆焊用金属粉末956
34.3.4 粉末等离子弧堆焊工艺958
34.3.5 粉末等离子弧堆焊的应用960
第35章 等离子弧焊应用实例962
35.1 板材对接焊962
35.2 直管对接焊963
35.3 薄壁容器的焊接964
35.4 薄壁小球的焊接965
35.5 不锈钢焊接管纵缝焊接966
35.6 单体液压支柱的焊接967
35.7 排气管的焊接968
35.8 管子对接全位置焊接969
35.9 波纹管和传感器的焊接969
35.9.1 波纹管的焊接969
35.9.2 波纹管与法兰的焊接970
35.9.3 压力传感器的焊接970
35.10 阀门密封面粉末等离子弧堆焊971
35.11 内燃机进排气阀密封面堆焊972
参考文献972